Recycle Bottle Washing Machine
Video
Description
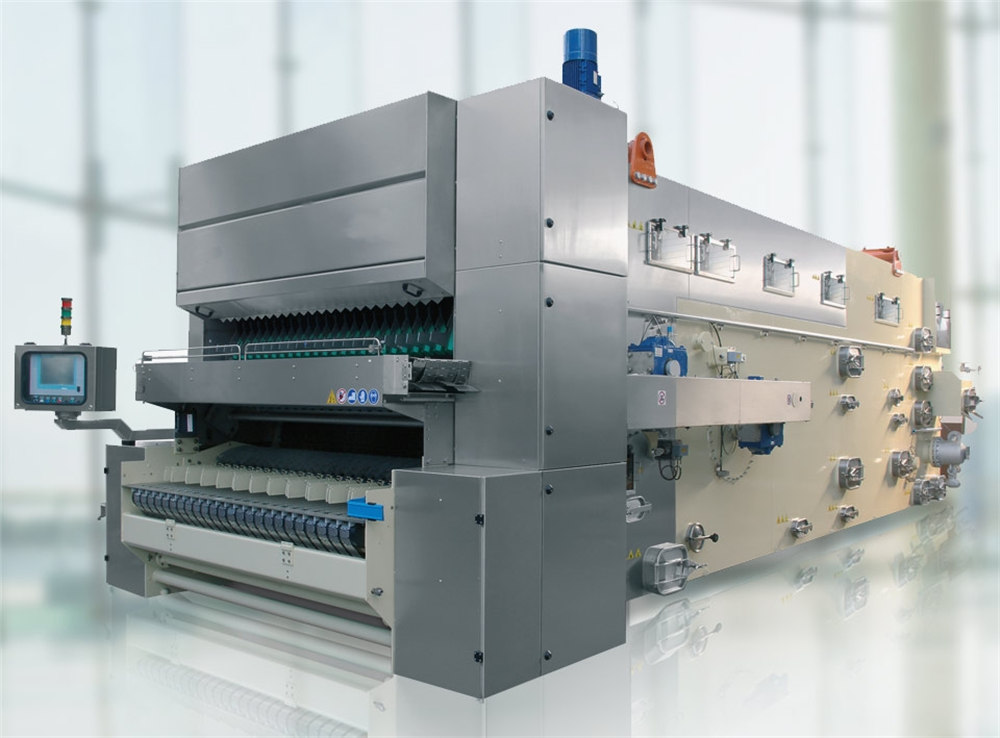
For milk, beer and cola companies with a high annual output, due to the large number of glass bottles in the packaging, but the cost of glass bottles is high, so these companies must recycle glass bottles to reduce the production cost. At GEM-TEC, you can get a variety of recycling bottle, recycling bin (case) cleaning solutions. The working flow of the bottle washing machine is as follows:
The cleaned bottles are transported to the bottle table of the washing machine by the bottle conveyor. After the arrangement of the bottle table is completed, the bottle is pushed into the bottle box of the bottle load rack driven by the main chain by the bottle feeding device. The bottle is first soaked in the soaking tank (according to the quality time of the bottle recovery is controlled within 8-12min, and the soaking time of the new bottle is 30s). Then after 13 internal spraying, five external spraying, (spraying process: first through eight circulating water spraying, then through three intermediate water spraying, and finally two fresh water spraying). Finally, the bottle discharging device sends the clean bottle to the bottle washing machine to complete the bottle washing process.
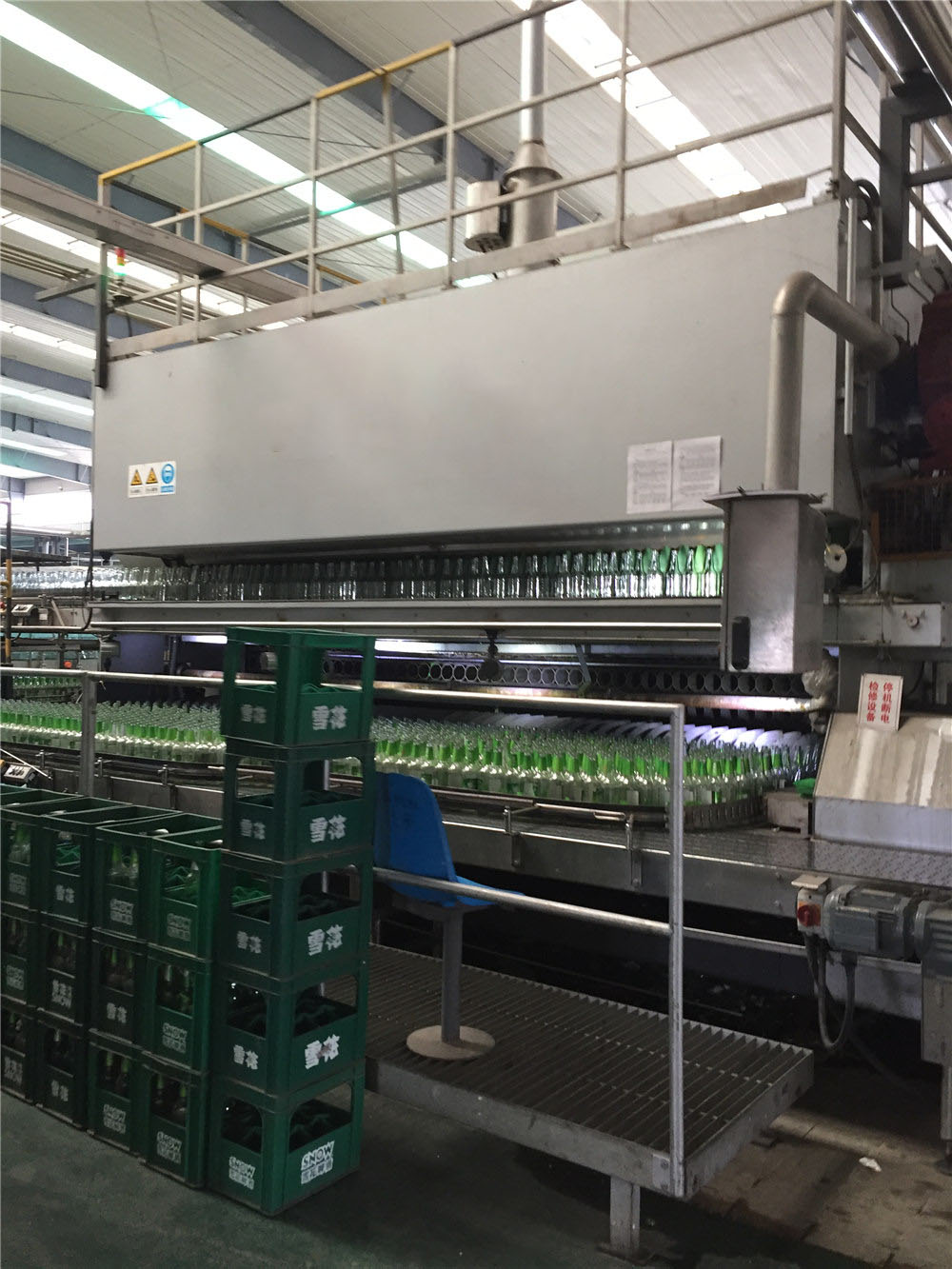
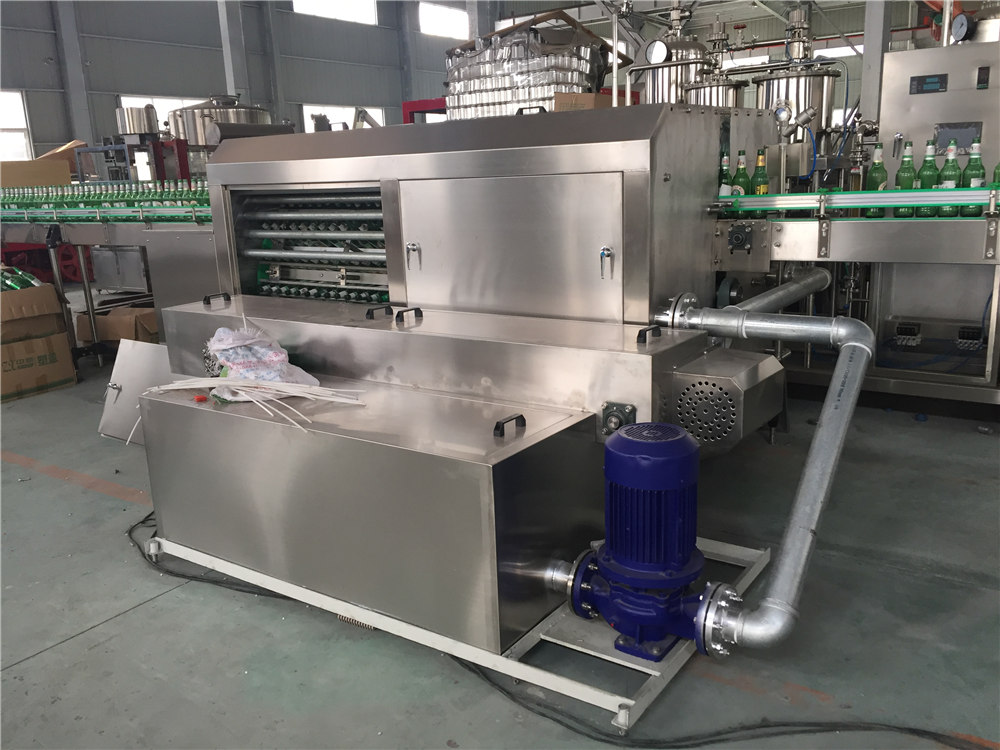
The bottle feeding mechanism adopts crank rocker and rotating working mechanism, which overcomes the dead point of the four-link mechanism and makes the bottle feeding stable and reliable.
The bottle release mechanism adopts the connecting rod to connect the bottle. The bottle is first connected by the cushion, and then the bottle is transferred to the bottle transport working face by the bottle catch claw. Finally, it is pushed to the bottle transport belt by the bottle catch guide rail.
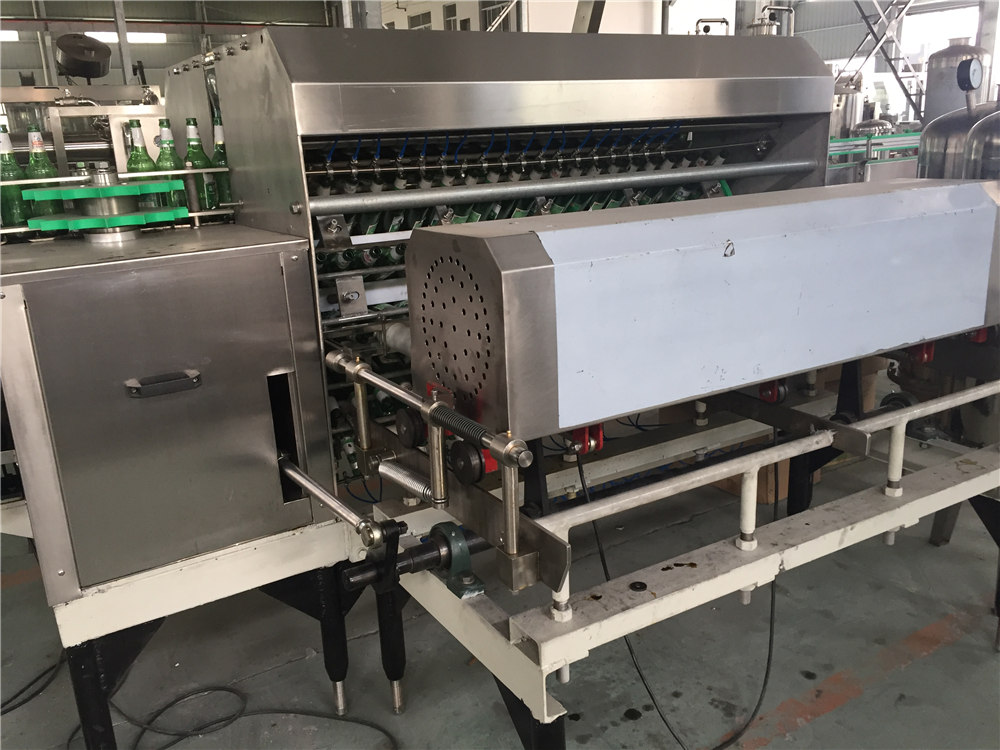
Features
1. The full plastic container not only reduces the overall weight of the bottle washing machine, but also can resist high temperature of 120° without deformation.
2. Equipped with alkali canister: you can pour alkali tablets into the alkali canister for stirring to convert solid into liquid for real-time addition of lye.
3. Lye online detection and addition: After the use of online alkali concentration detection instrument, it can reduce the labor intensity of operators and effectively control alkali concentration.
4. Trademark press: Press the old label paper removed from the bottle washing machine through this machine to reduce its moisture and volume, and facilitate the transportation of the pressed label. This pressing machine will be 94% of the water content of the old label paper is squeezed, the water content of the squeezed label is only about 6%. At the same time, the equipment has a wide range of pressing pressure capacity, which can meet the requirements of different output of bottle washing machines, up to 76000BPH production line. The equipment has the advantages of small space occupation, strong power, low energy consumption, simple structure, convenient maintenance, energy saving and reduce environmental pollution, and so on. It is praised by the majority of domestic users at present!
5. Equipped with lye online filter: it is a kind of separation of the label paper, fiber and other impurities in the lye circulation process, to ensure that the spray head is not blocked in the lye circulation process, in order to achieve high efficiency and save the circulation of lye, control system (PLC PAC) intelligent design, can automatically identify the degree of label paper deposition, automatic cleaning sewage. The device is composed of a Double isolation (DIS) system that separates lye labels accurately and an IC system that controls the operation of the DIS system.
6. Equipped with automatic backwash function: reduce the probability of clogging spray pipe.
7. Follow the spray mechanism to ensure that every corner of the bottle is cleaned.
8. Transmission can be reliable mechanical structure, or can be electric synchronous transmission.
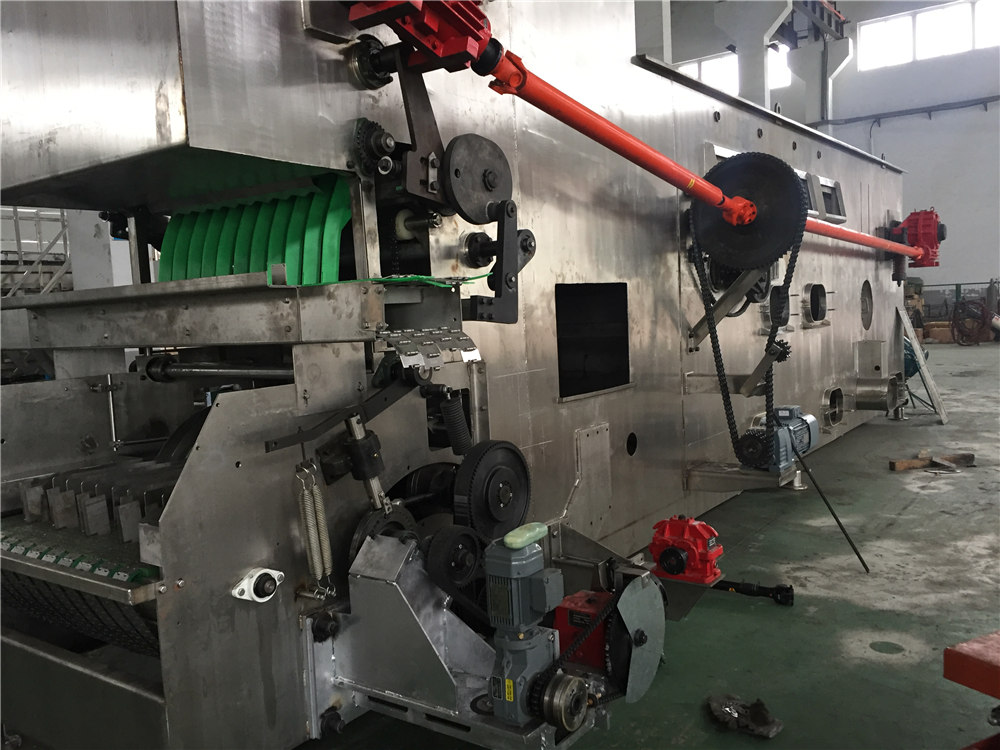
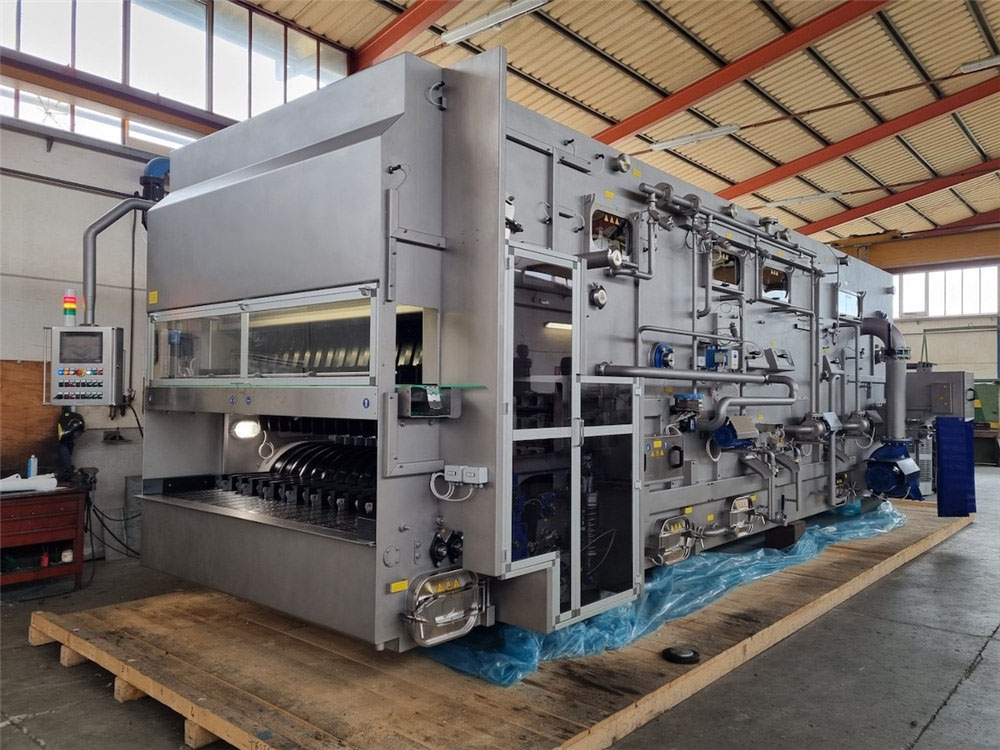
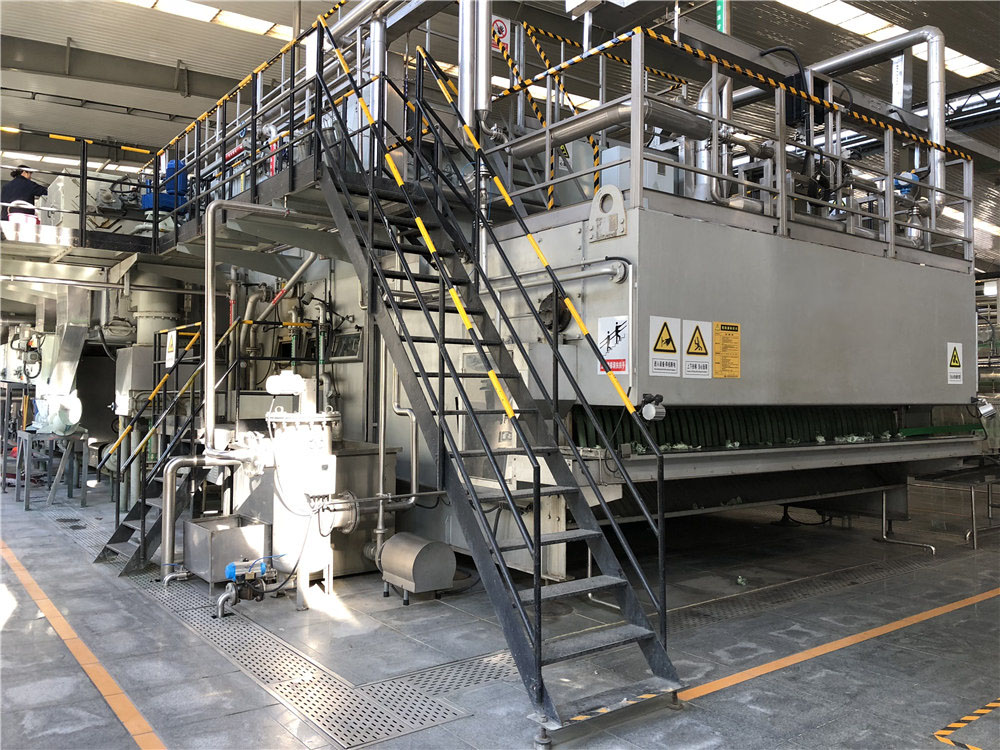
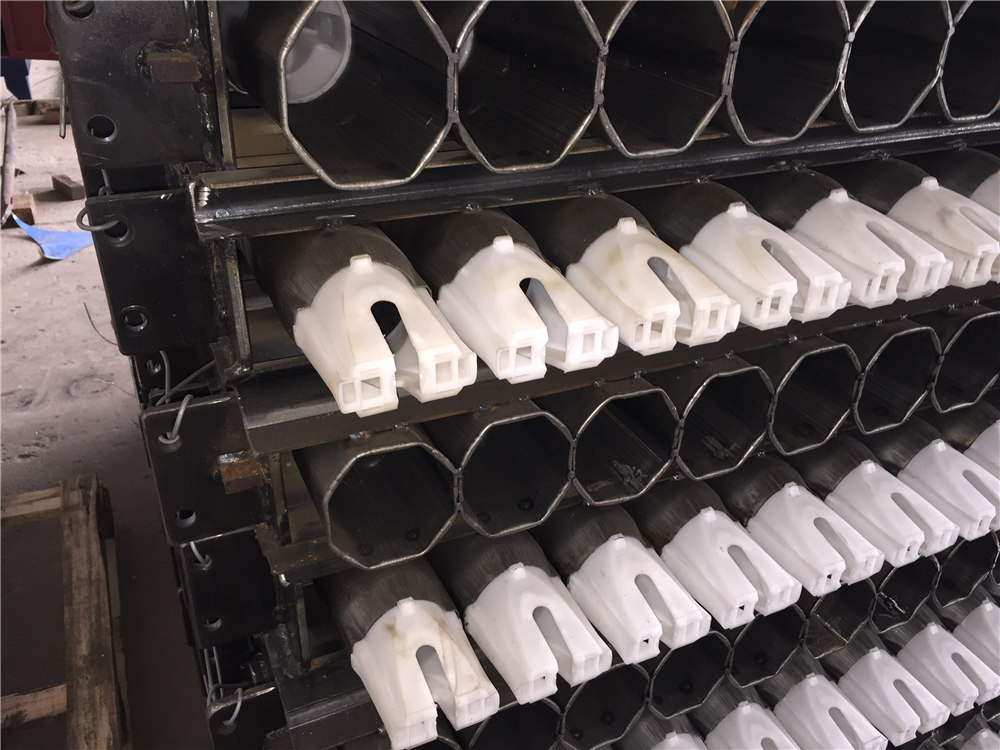
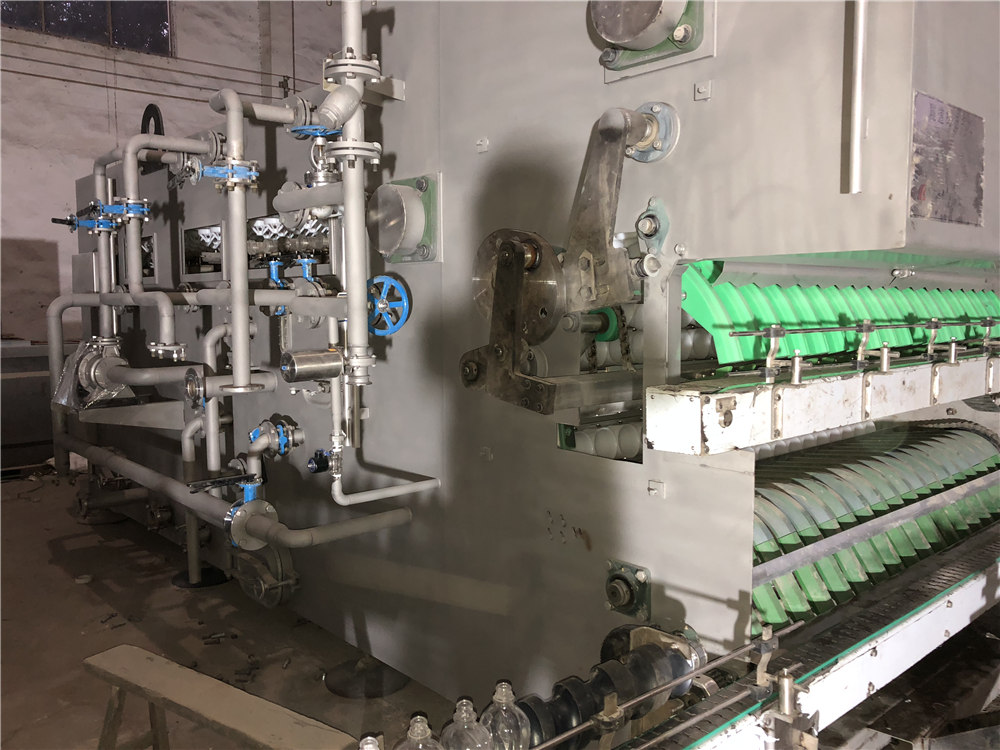
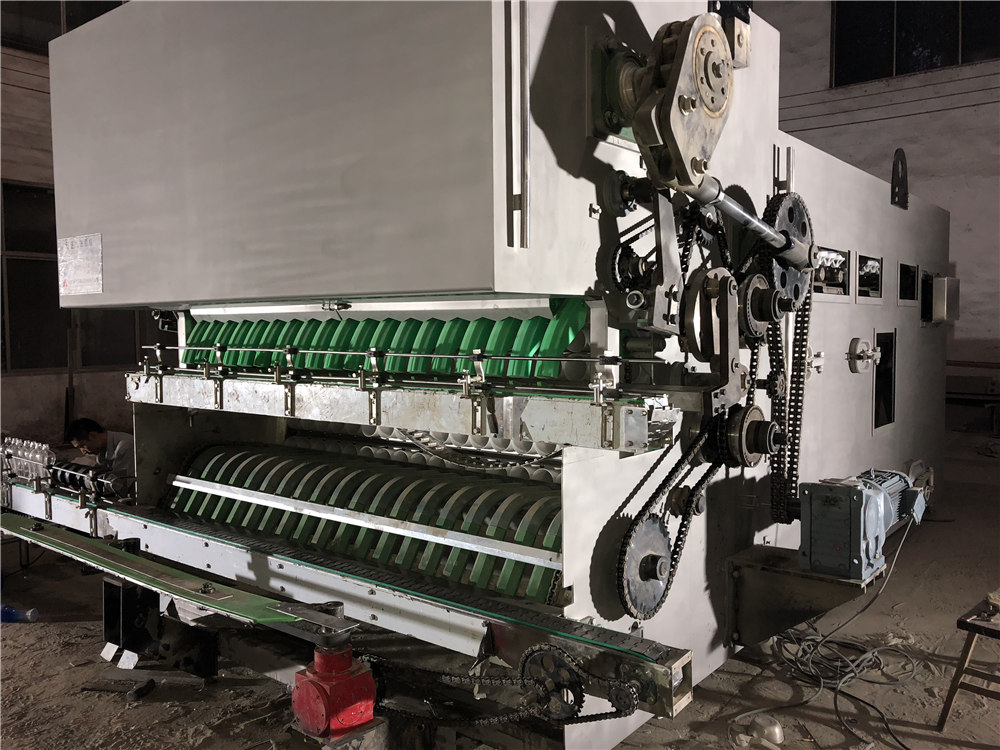
Production Capacity
Production Capacity: 6000-40000 bottles /H
Structure
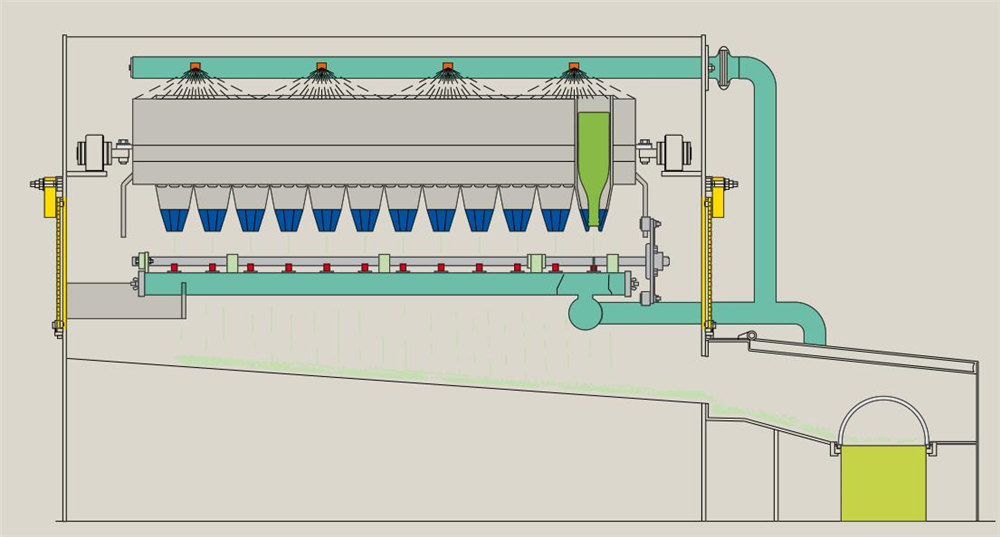
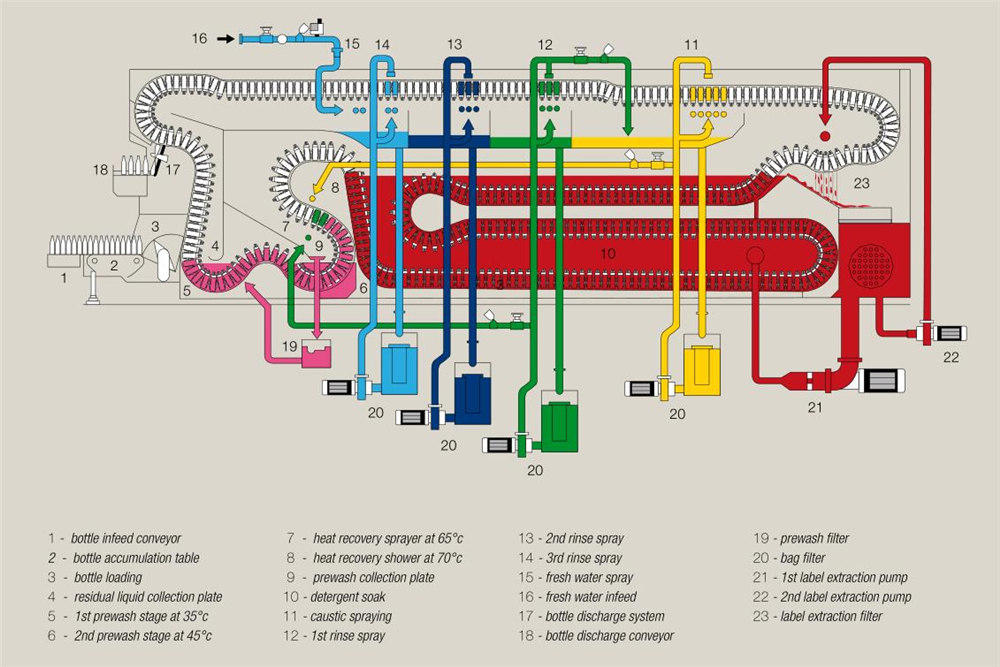