Filling Machine for Daily Chemical Products
Description
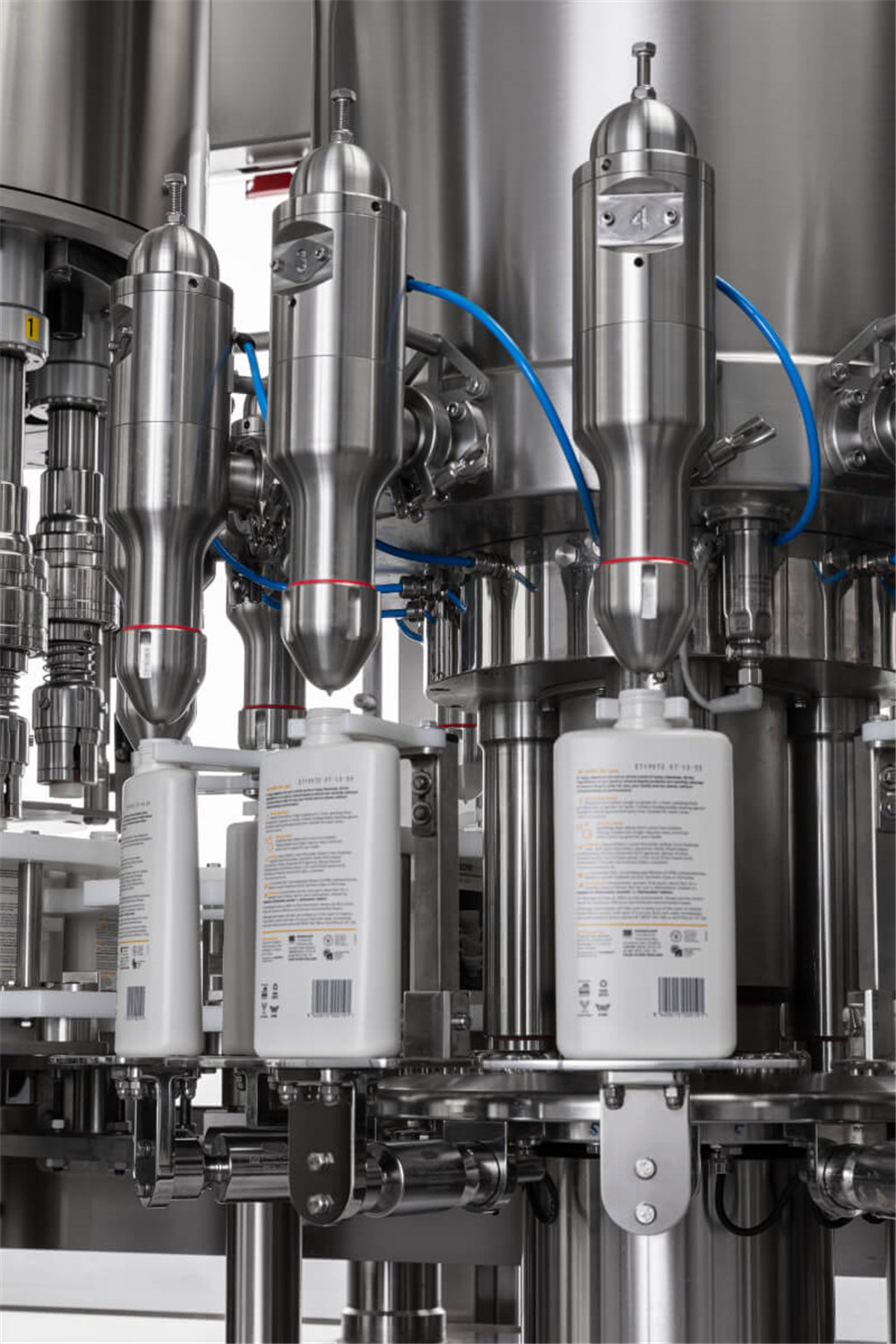
Daily chemical products are closely related to our daily life. With the growth of economy and the improvement of people’s living standard, the market scale of daily chemical industry is getting bigger and bigger. Daily chemical products mainly include washing products and oral care products and so on. As a more traditional industry, the product categories of daily chemical products industry are complex, such as laundry detergent, dish soap, shampoo, disinfectant and conditioner, etc. The bottles and caps of these products are often varied and irregular, with different packaging containers; At the same time, there are many technical difficulties in product filling such as bubbling, wire drawing and dripping; Filling accuracy and hygiene requirements are also very demanding; Production capacity is also a new trend for filling equipment to put forward new requirements.
GEM daily chemical solutions take into account key points in each production environment, with our core technology and rich practical experience can provide high standard solutions according to the processing technology you need, make your entire production process more safe and easier to operate.
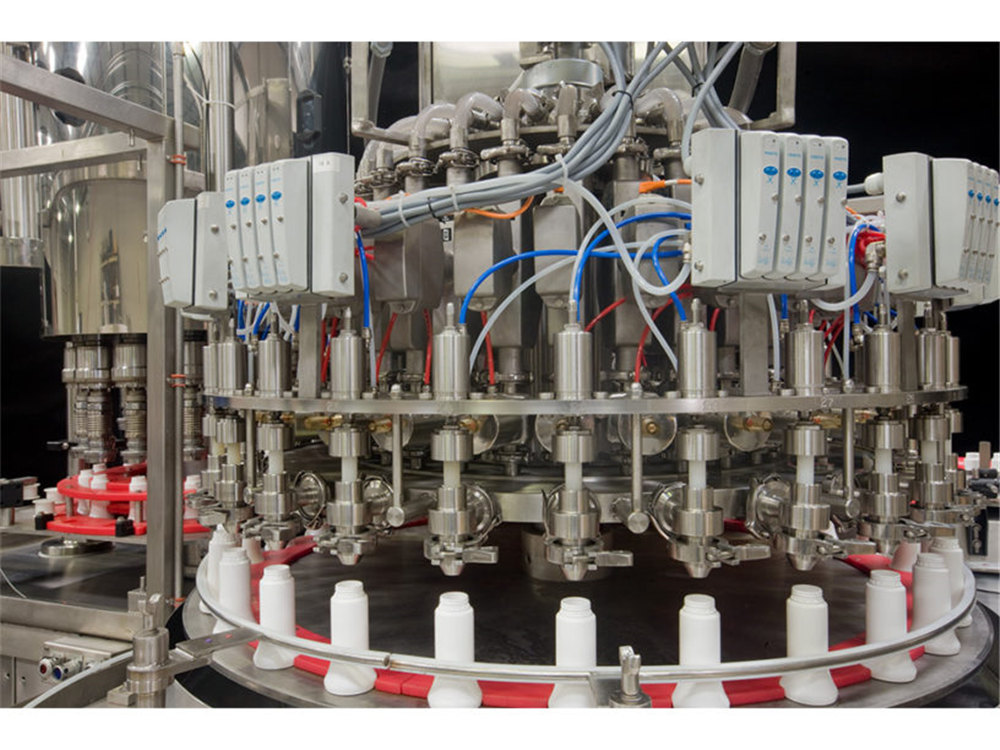
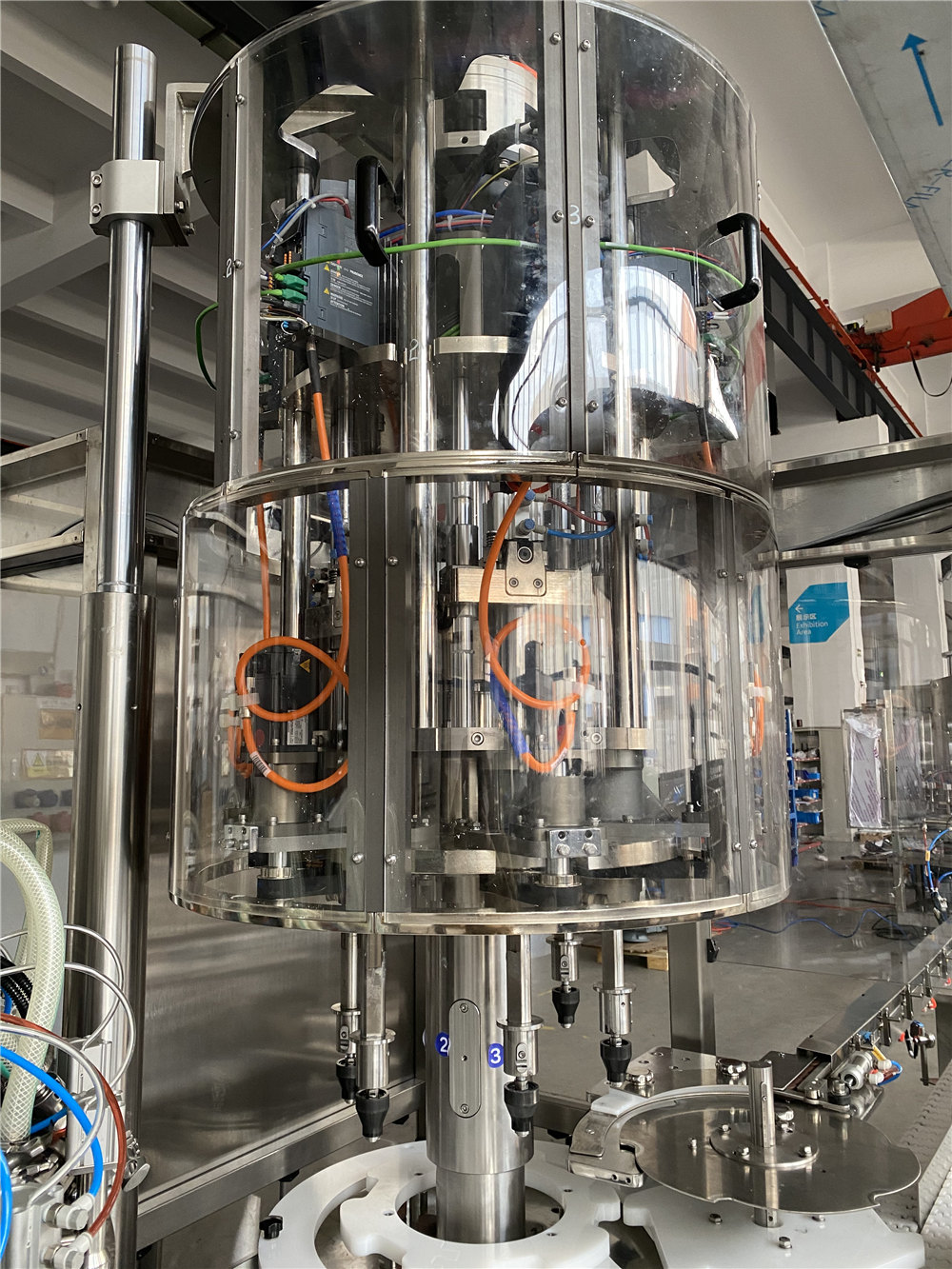
The filling of daily chemicals is similar to that of oil, filling methods are mainly piston volumentric filling or provide electromagnetic flowmeters for conductive liquids and mass flowmeters for non-conductive liquids. The main difficulty of filling is to solve the problem of accurate measurement, no drip, bubbling, wire drawing and so on. Because of the variety of bottles used in filling daily chemical products, the convenience of changing bottle type should be considered in the disign. The diversity of packaging containers also detemines that there are many kinds of LIDS, such as gun caps and pump heads, these caps have a special shape and hold a long tube underneath, so the lid will be different from other types. The sealing of daily chemical products mainly uses traditional permanent magnet torque control or servo torque control form, the manipulator adopts three claws or four rollers. The servo torque contorl form carries out closed loop control through the servo notor and program in the whole capping process, the servo motor can also control the curve motion of the cap to realize the torque control of the digital cap.
Machine Features
1. Unique drip free and anti-bubbling filling valve design, the material will not drip to the bottle mouth or shoulder, no product overflow during the filling process.
2. Precise quantitative control, piston cylinder type/induction type electromagnetic flowmeter (positive displacement filling) or mass type (weight/weighing flowmeter filling), positive pressure/ gravity filling mode.
3. Siemens control system is adopted, with high automatic control ability, all parts of the function of automatic operation, no operation after startup.
4. The machine transmission adopts modular design, frequency conversion stepless speed regulation, wide speed range. The drive is equipped with automatic lubricating grease device, which can supply oil to each lubricating point according to the need of timing and quantity, with sufficient lubrication, high efficiency, low noise and long service life.
5. The height of the material in the filling cylinder is detected by the electronic probe, and the PLC closed-loop PID control ensures stable liquid level and reliable filling.
6. The material channel can be cleaned CIP completely, and the workbench and the contact part of the bottle can be washed directly, which meets the sanitary requirements of filling; Can be used according to the need of single-sided tilt table; Custom automatic CIP fake cups are also available.
7. According to the requirements of different products, filling method and sealing type can be matched at will.
8. The filling valve is not in contact with the bottle during the filling process to avoid cross contamination.
9. No mechanical CAM is needed for capping. When changing the production variety or adding new varieties, you only need to switch or add the CAM curve, which greatly improves the production efficiency and mechanical flexibility.
10. The position of the cap lifting shaft can be monitored in real time in the system, and the data can be mastered in real time. These data can also be used for capping process control.
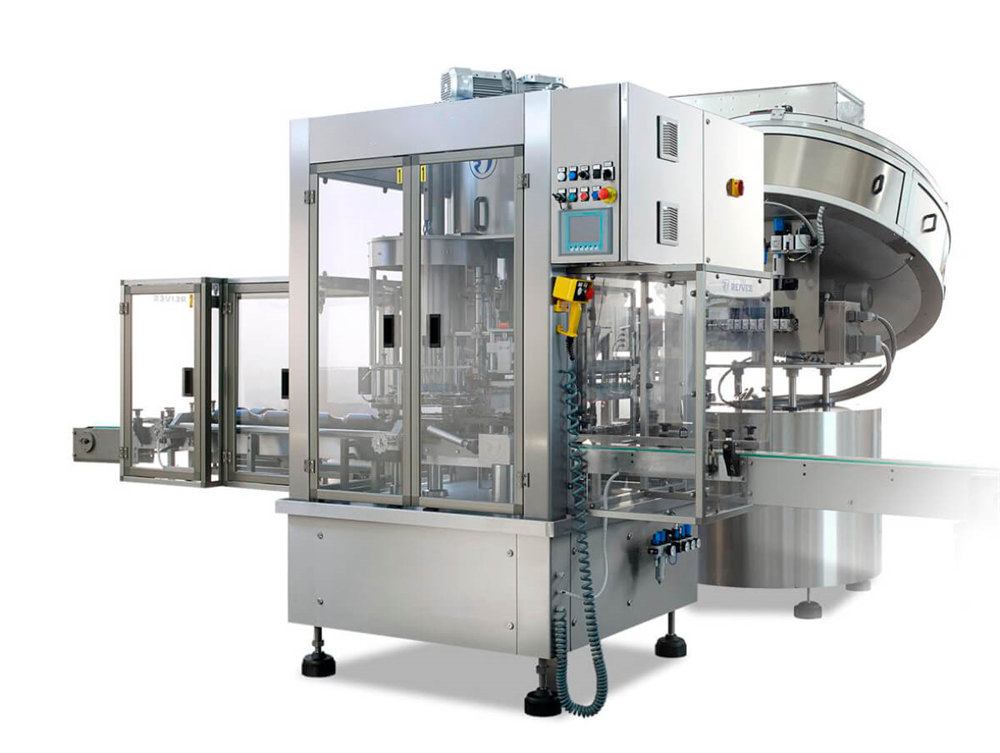
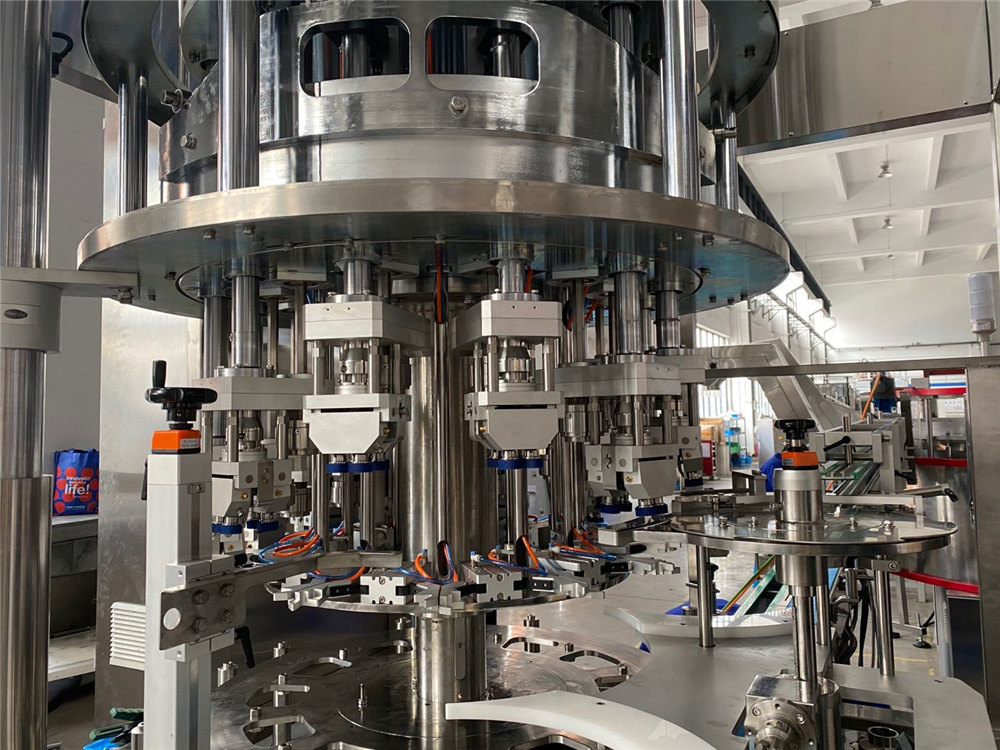
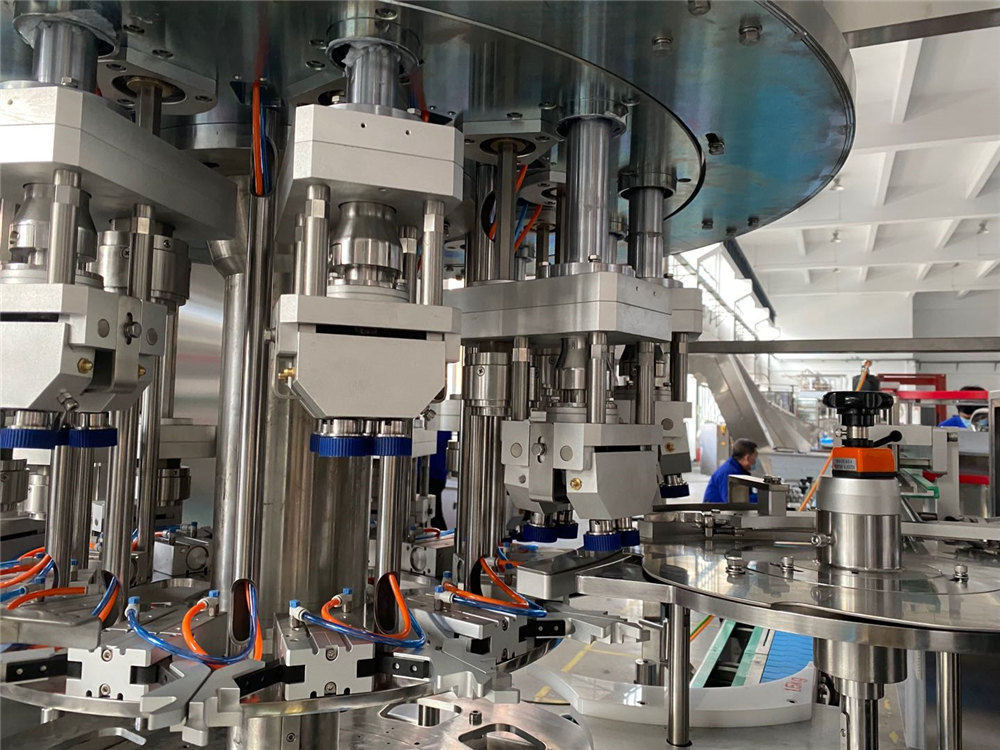
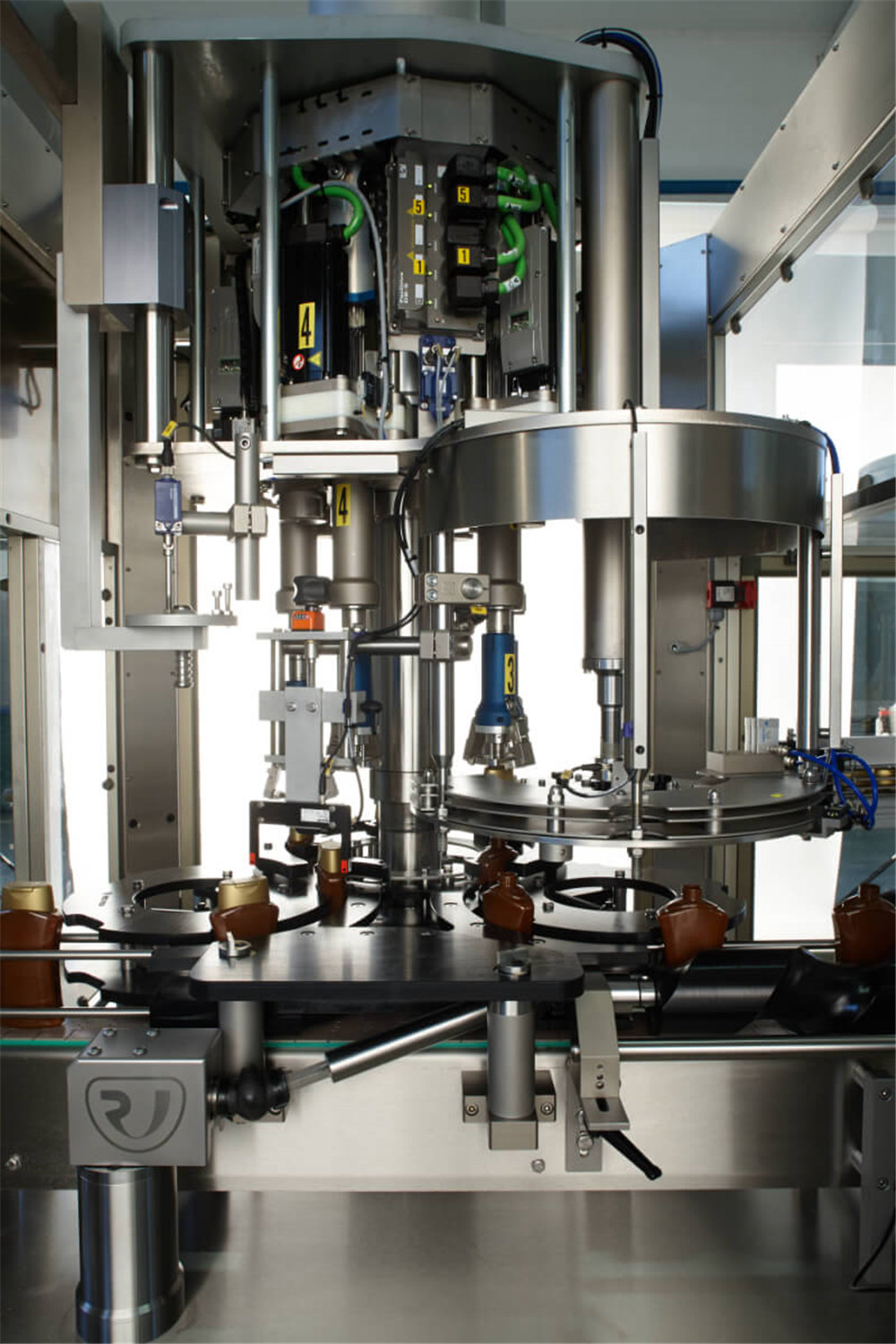
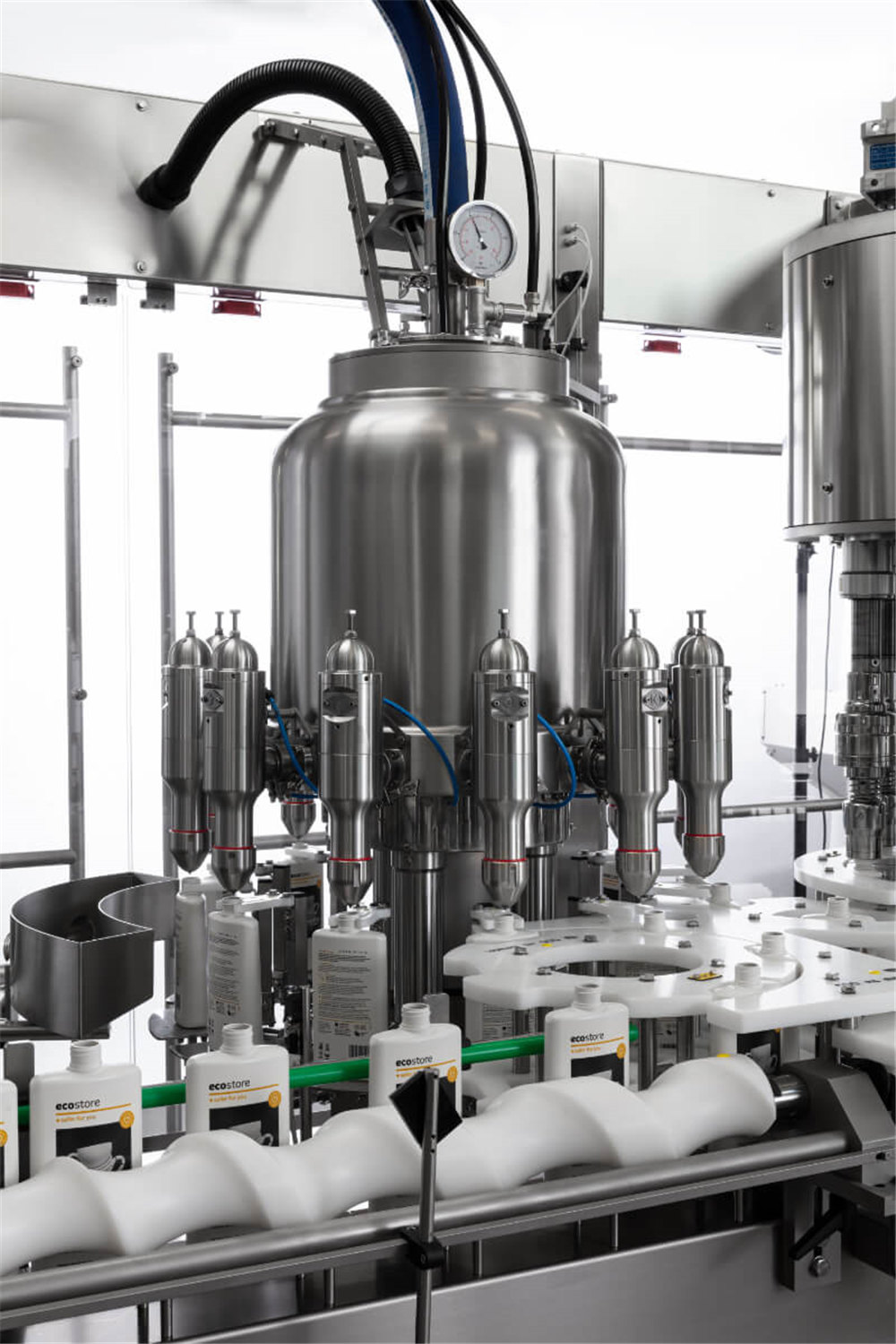
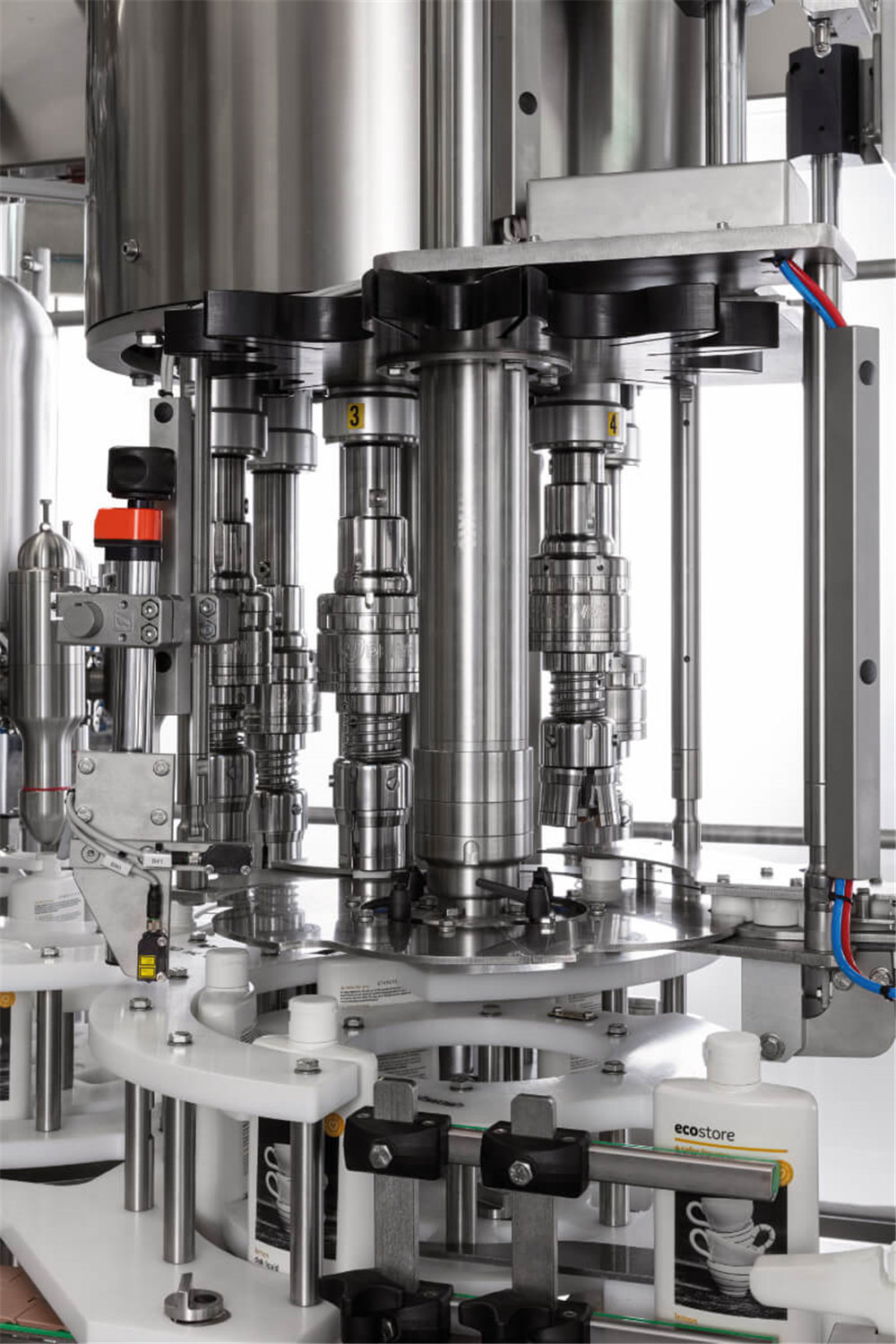
Parameter
No. |
Model Series |
Material Viscosity range CPS |
power |
Equipped with air source |
Equipped with power source |
Conveying line height
|
suitable for bottle type range |
01 |
JH-CF-6 |
0-200 |
3Kw |
5-6bar |
380V |
1000±50mm |
Customized according to customer needs
|
02 |
JH-CF-8 |
0-200 |
3Kw |
5-6bar |
380V |
1000±50mm |
|
03 |
JH-CF-10 |
0-200 |
3.5KW |
5-6bar |
380V |
1000±50mm |
|
04 |
JH-CF-12 |
0-200 |
3.5KW |
5-6bar |
380V |
1000±50mm |
|
05 |
JH-CF-14 |
0-200 |
4.5Kw |
5-6bar |
380V |
1000±50mm |
|
06 |
JH-CF-16 |
0-200 |
4.5Kw |
5-6bar |
380V |
1000±50mm |
|
07 |
JH-CF-20 |
0-200 |
5Kw |
5-6bar |
380V |
1000±50mm |