Automatic Glass Bottle/ Can Beer Filling Machine
Video
Description
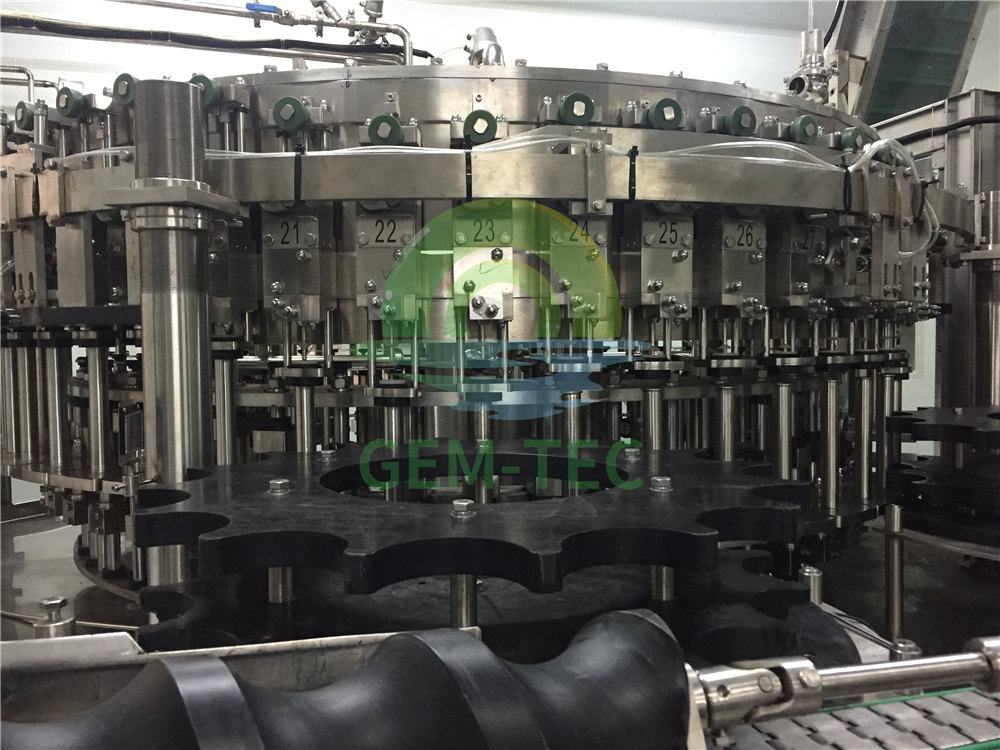
Beer is one of the oldest alcoholic drinks in the world, and even now it is the most popular alcoholic drink in many countries, with various traditional activities associated with drinking beer. In recent years, the “high-end” craft beer began to appear more and more in the market and consumers. Unlike industrial beers, craft beers focus on taste and flavor, leading to a richer, fresher drinking experience. Craft beer has attracted the attention of many young people with its strong malt flavor and rich taste, and has gradually become popular.
GEM-TEC provides brewers with 1000-24000BPH beer filling machines, as well as filling solutions for small volume, high CO2 content, and foamier beers specifically targeted at craft beer customers.
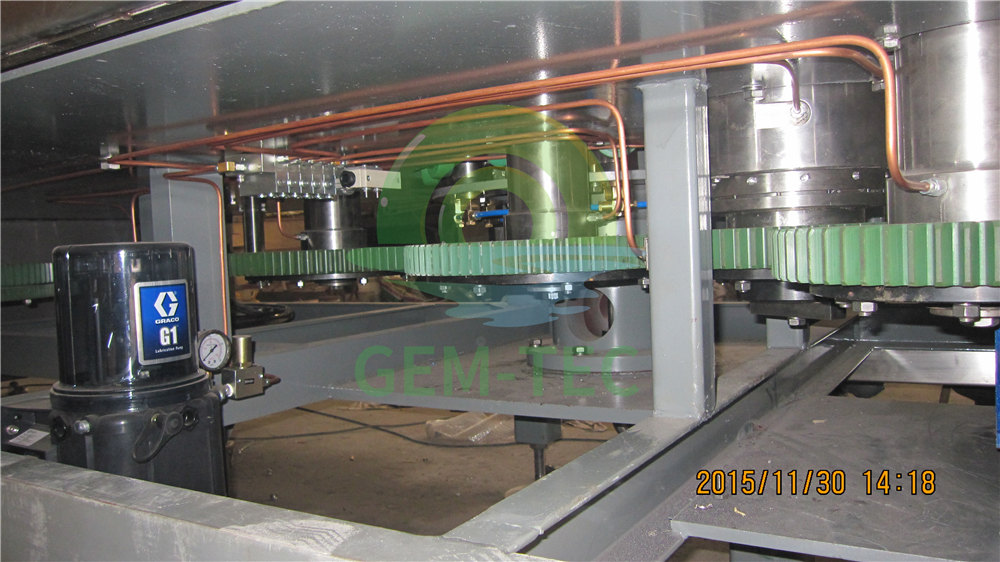
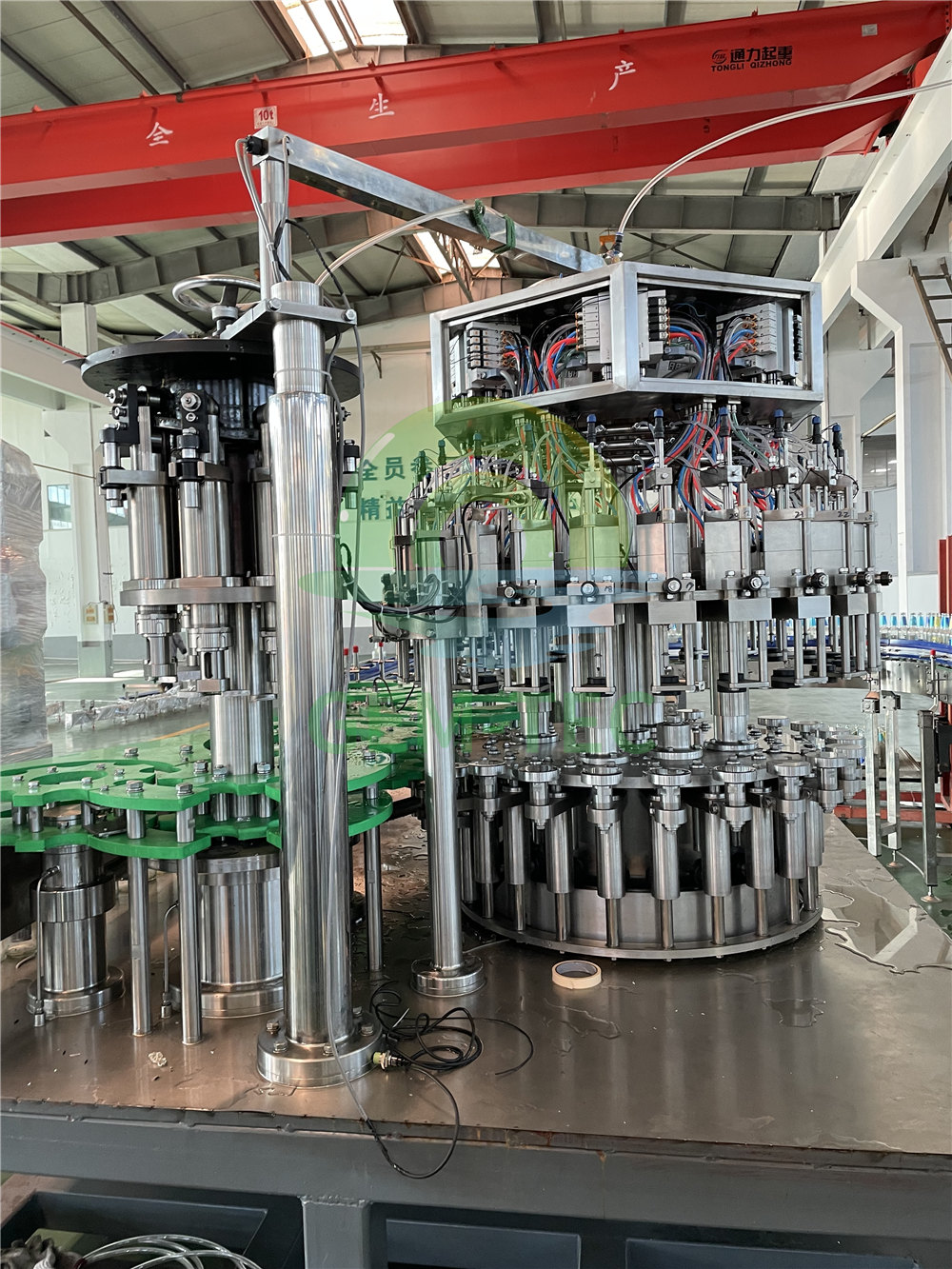
JH-PF Beer filling machine is suitable for bottle beer filling as well as cocktails or other alcoholic beverages. Adopt reliable isobaric filling technology. Our filling technology can help your brand increase bottling production in an economical and fast way. Conventional models use stable and easy to clean mechanical filling valves, including open and close valves, CO2 purge, CO2 inflation, post-filling pressure relief are all controlled by mechanical cams. The mechanical structure of each part ensures the stability of the filling process. At the same time, it also adds a vacuum-pumping device to the bottle before filling for several times to reduce the air and oxygen in the bottle as far as possible. Which reduces the oxygen increase in beer; After filling, high temperature and high pressure sterile water is used to bubble the beer at high pressure, and the resulting foam will drive out the air in the bottle neck. When a small amount of foam overflows the bottle mouth, the bottle cap will be sealed. These measures can greatly ensure that the beer will not be oxidized, and ensure the beer fresh and pure taste.
Filling Cycle Process
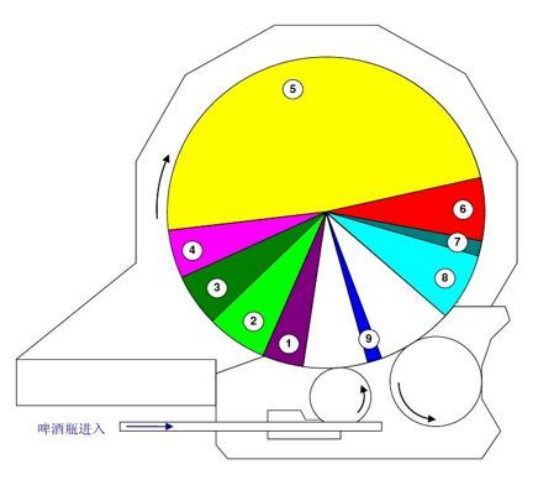
① The first vacuum
② CO2 flushing
③ Vacuum the second time
④ Backup pressure
⑤ Filling
⑥ Filling/precipitation completed
⑦ Valve closure
⑧ Pressure relief and exhaust
⑨ Valve purge
Technical Structure Features
1. Filling valve adopts high precision mechanical filling valve. (Optional electronic valve level valve/electromagnetic flowmeter valve)
2. The whole machine has two vacuum pumping capacity, no bottle no vacuum function.
3. In the flushing or filling, due to the bottle quality problems caused by the bottle burst, the filling valve is automatically closed, and there is a broken bottle automatic flushing device.
4. Equipped with high pressure hot water bubble device, to reduce the bottleneck air content and beer dissolved oxygen.
5. The machine transmission adopts modular design, frequency conversion stepless speed regulation, wide range of speed regulation. The drive is equipped with automatic lubricating grease device, which can supply oil to each lubricating point according to the need of timing and quantity, with sufficient lubrication, high efficiency, low noise and long service life.
6. The back pressure of the material in the filling cylinder can be automatically controlled, and its working conditions and parameters can be displayed on the control cabinet.
7. The height of the material in the filling cylinder is detected by the electronic probe. PLC closed-loop PID control ensures stable liquid level and reliable filling.
8. The height of the filling cylinder and control ring can be adjusted to suit the filling of containers of different sizes within the design range.
9. The use of all stainless steel cover hopper, the cover of the cover, the cover, into the cover transmission is reliable, in the operation of the cover is not easy to deformation, large and unobstructed cover.
10. The gland is reliable; And has automatic unloading function, reduce the broken bottle rate.
11. Adopt Siemens control system, with high automatic control ability, all parts of the function of automatic operation, no operation after starting (such as: filling speed follow the whole line speed, liquid level detection, liquid inlet regulation, bubble pressure, lubrication system, cover conveying system)
12. The material channel can be cleaned CIP completely, and the workbench and the contact part of the bottle can be washed directly, which meets the sanitary requirements of filling; Can be used according to the need of single-sided tilt table.
13. A variety of sealing methods (such as: crown cover, pull ring cover, metal or plastic anti-theft cover, etc.)
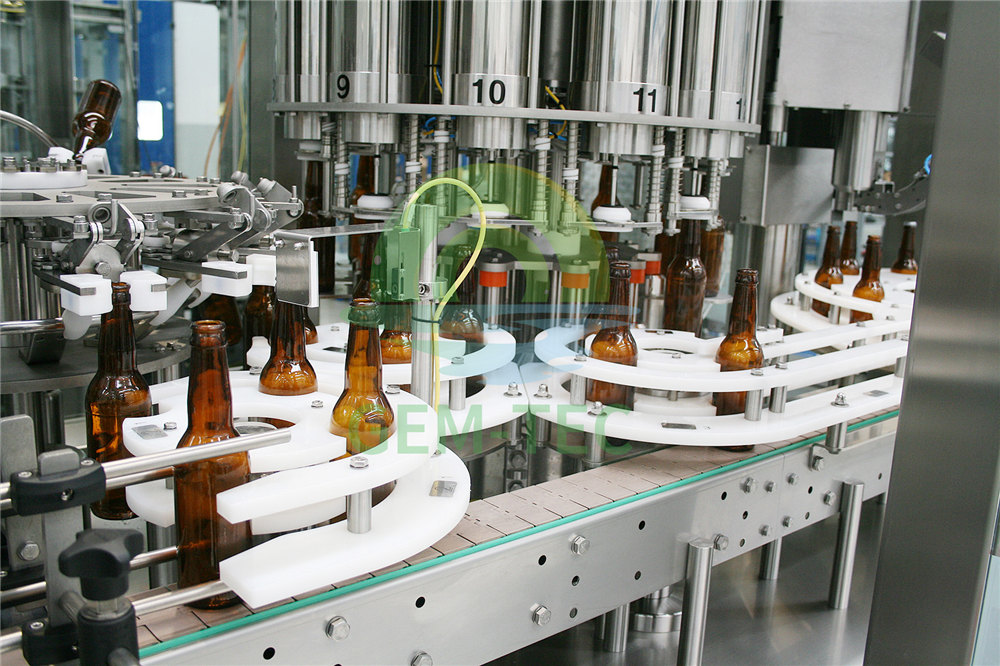
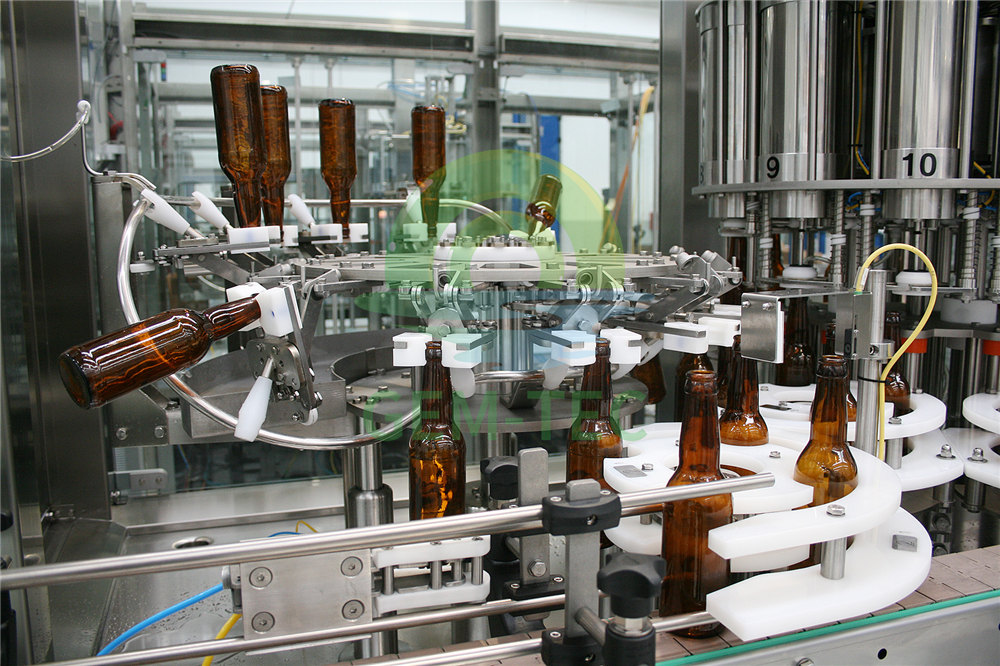
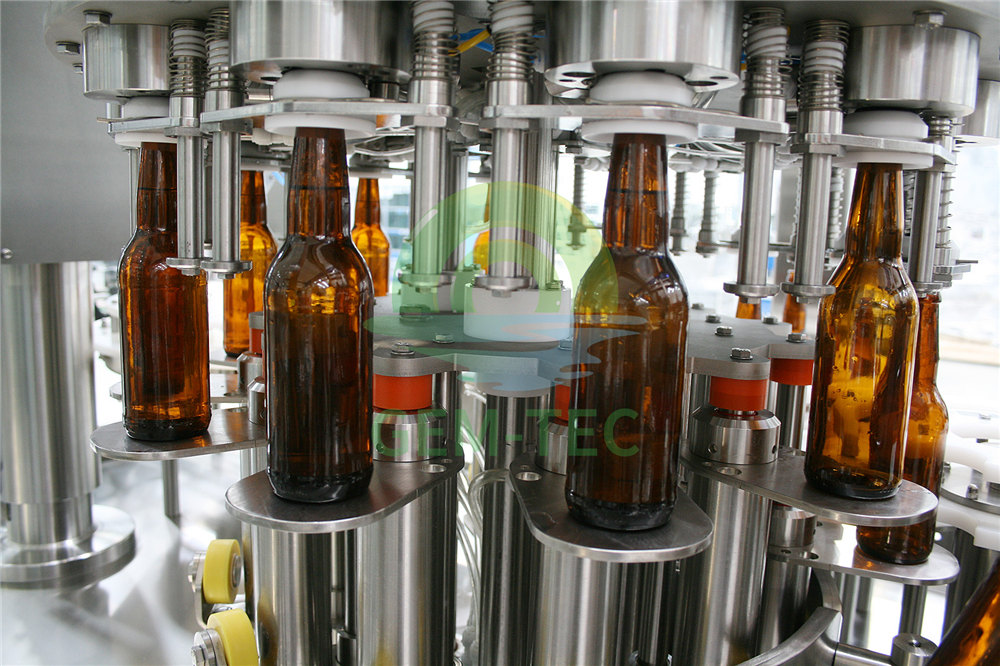
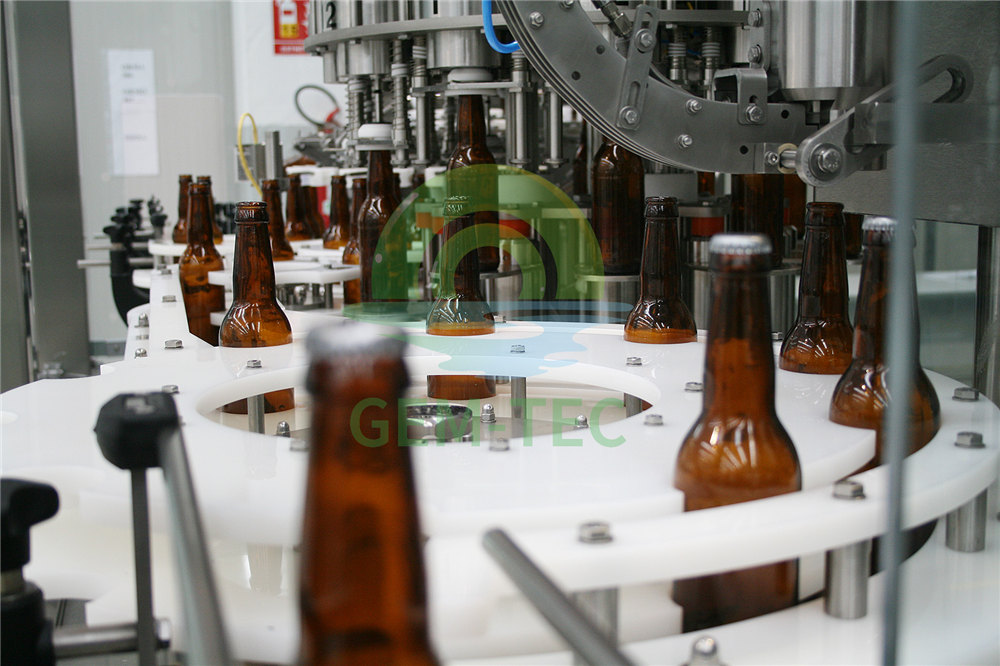
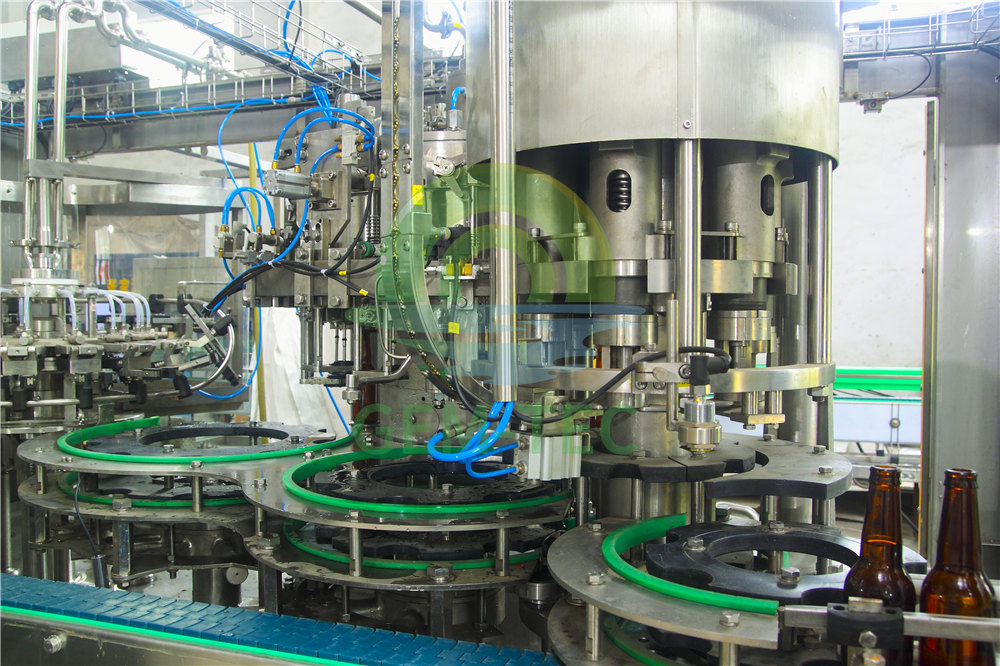
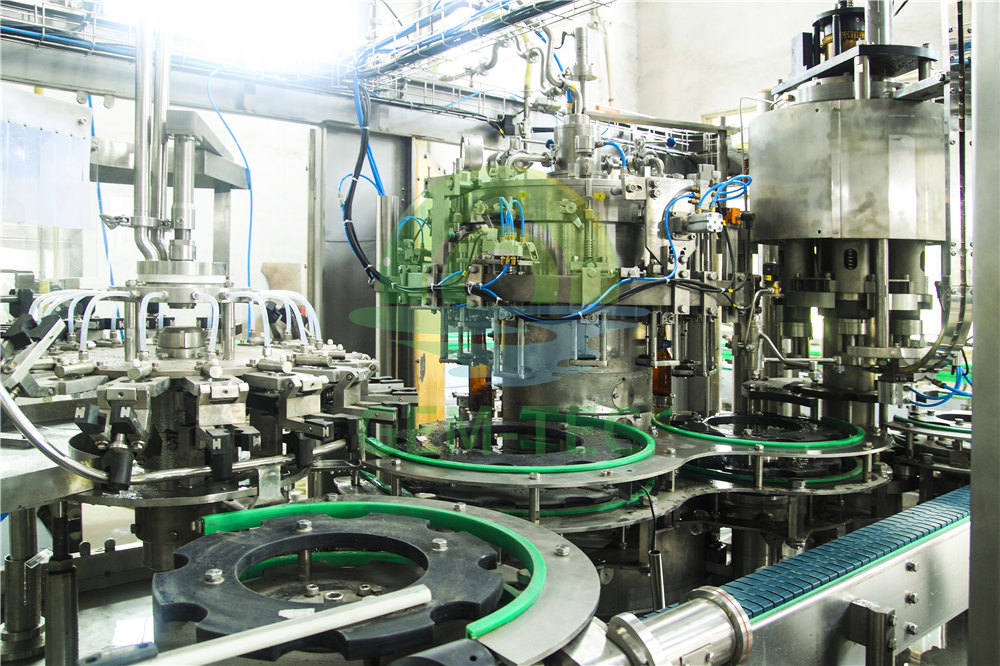
According to the requirements of different users and different products, filling valve can also use electronic filling. This filling method controls the opening and closing of the beer valve, vacuuming, exhaust pressure relief and other actions are pneumatic control, and the filling flow rate can be adjusted appropriately. The structure is more simple, reliable and easy to maintain. You can also customize the fully automatic CIP function, cleaning fake cups automatically mount, no manual operation is required.
For customers who require accurate filling volume, electronic quantitative filling valve can be used to change the capacity. As long as the filling speed is adjusted on the HMI, accurate switching can be achieved.
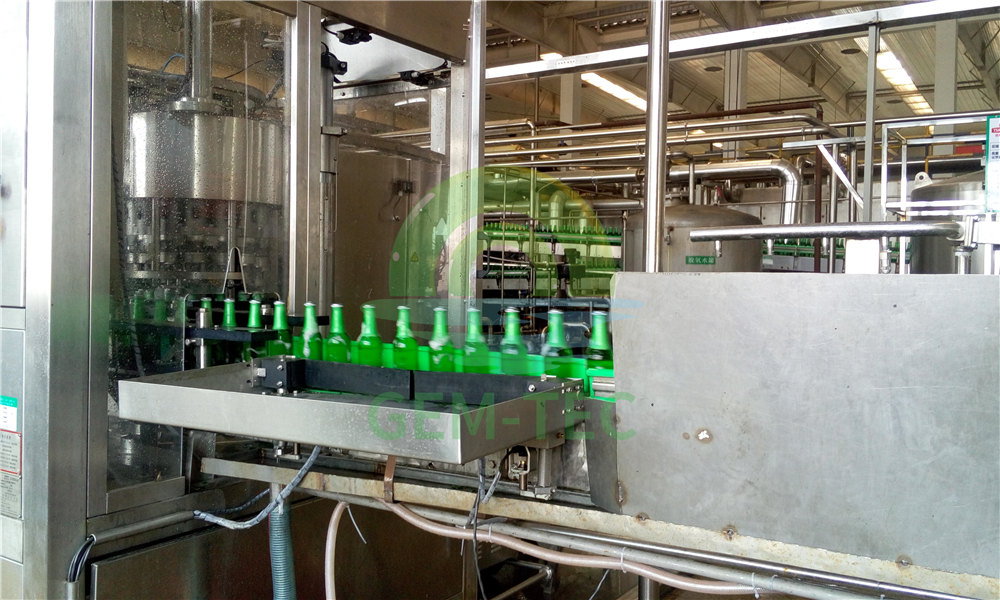
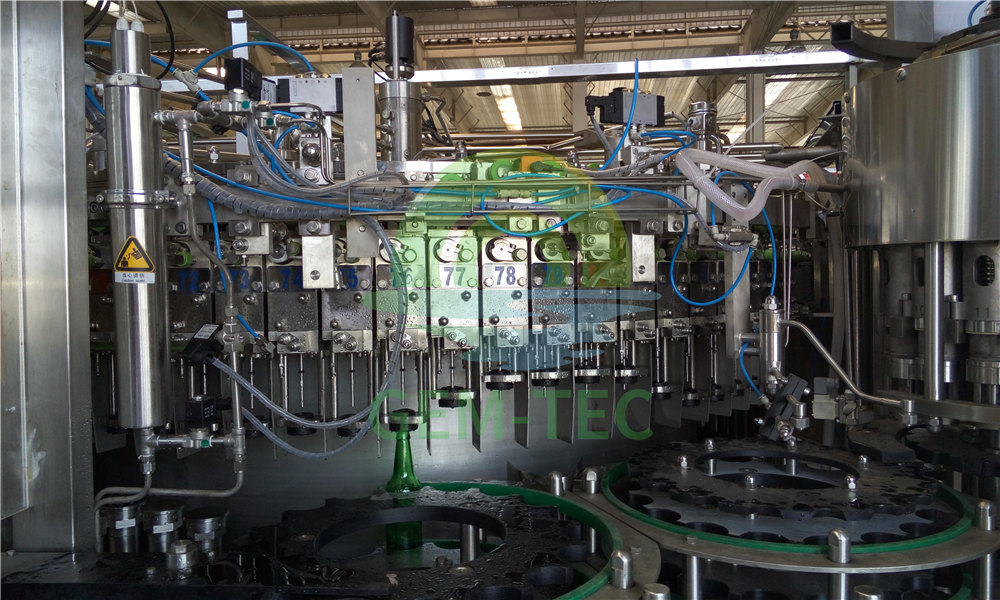
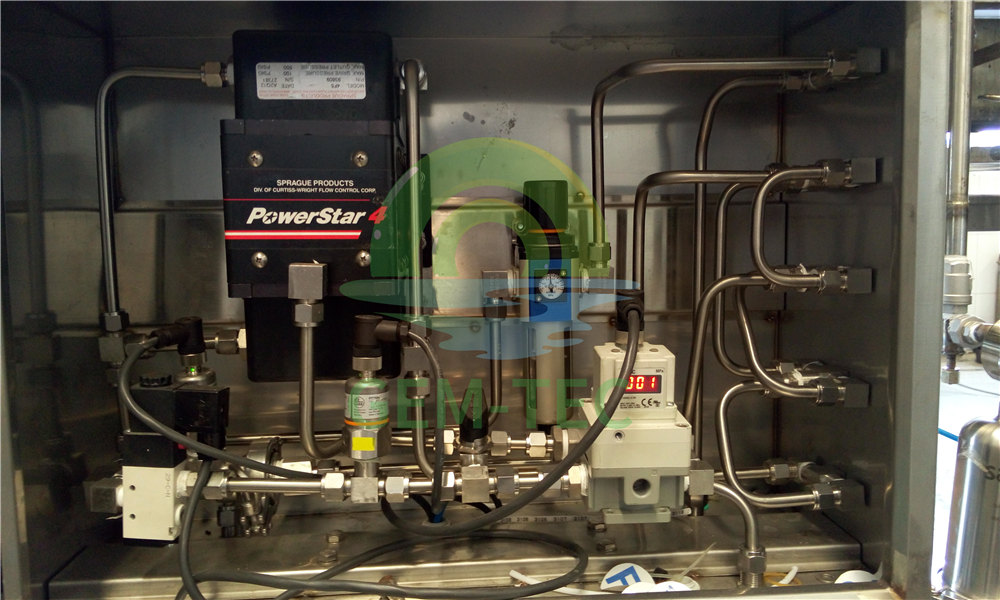
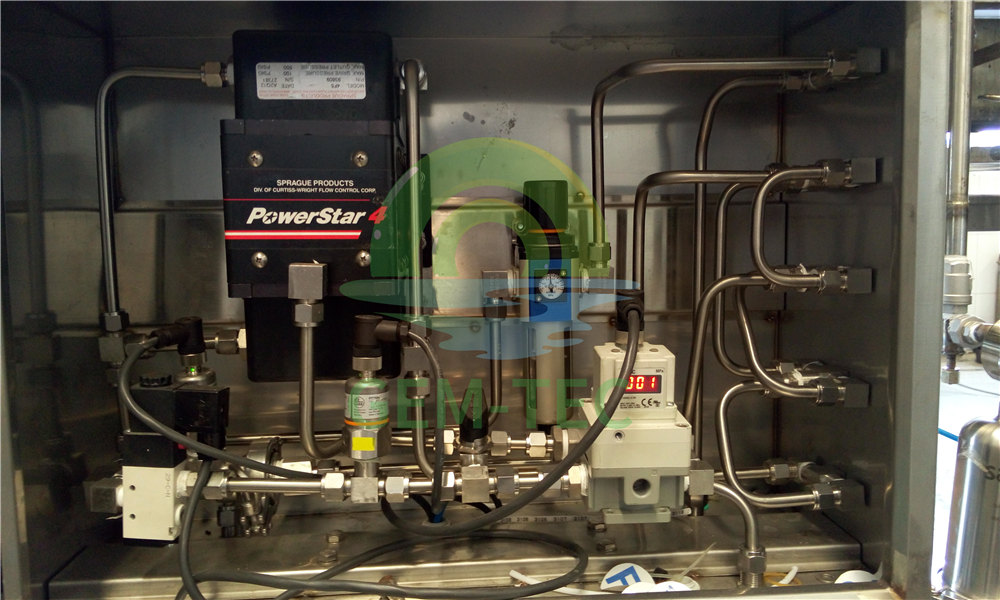
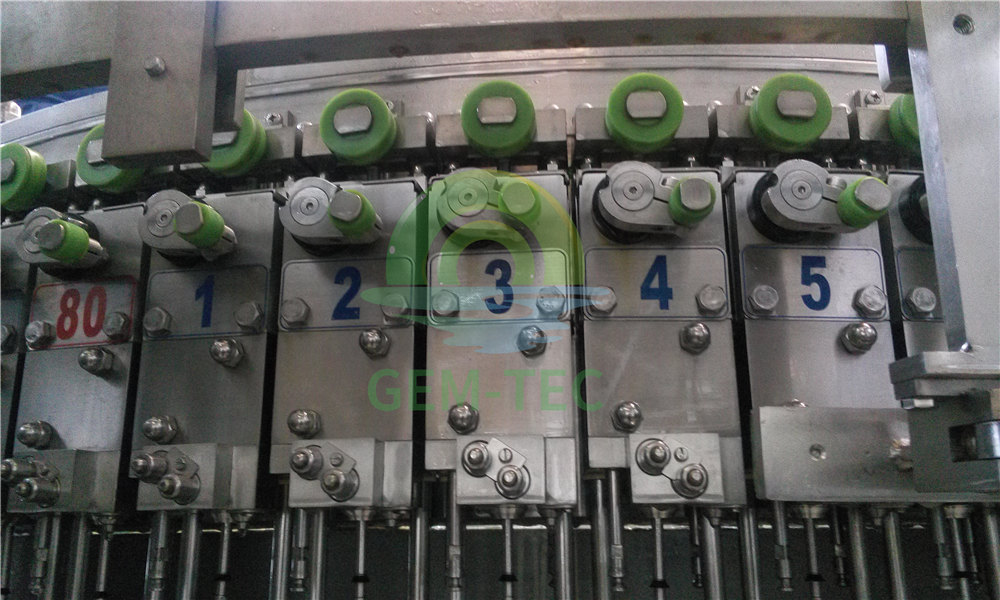
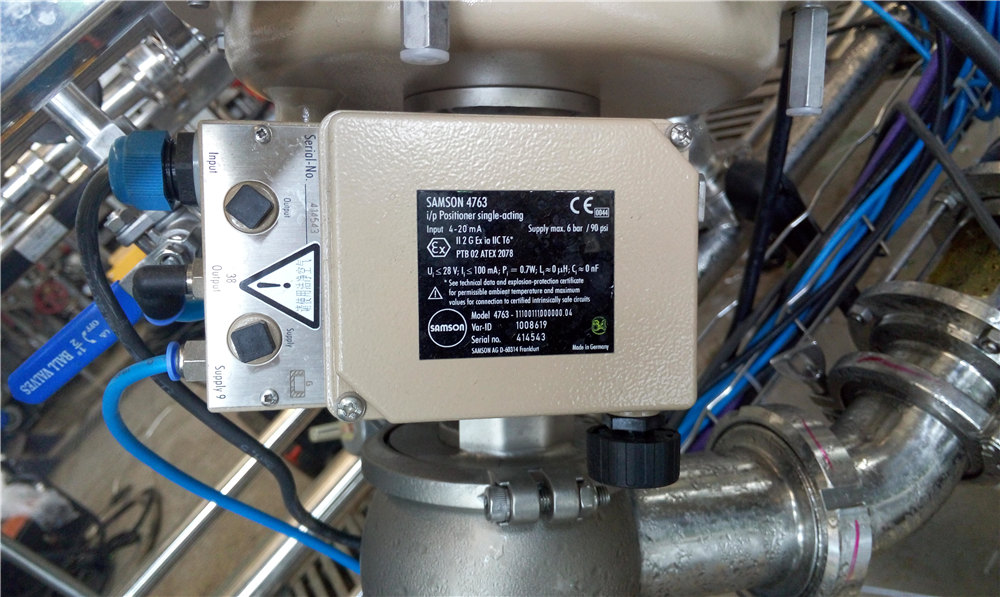
Structure
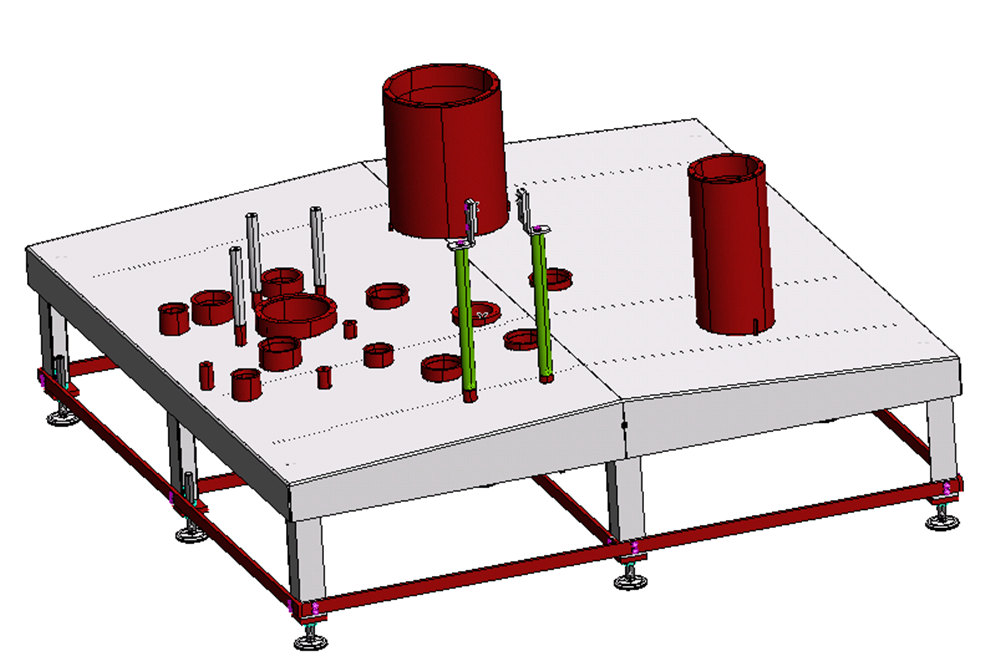
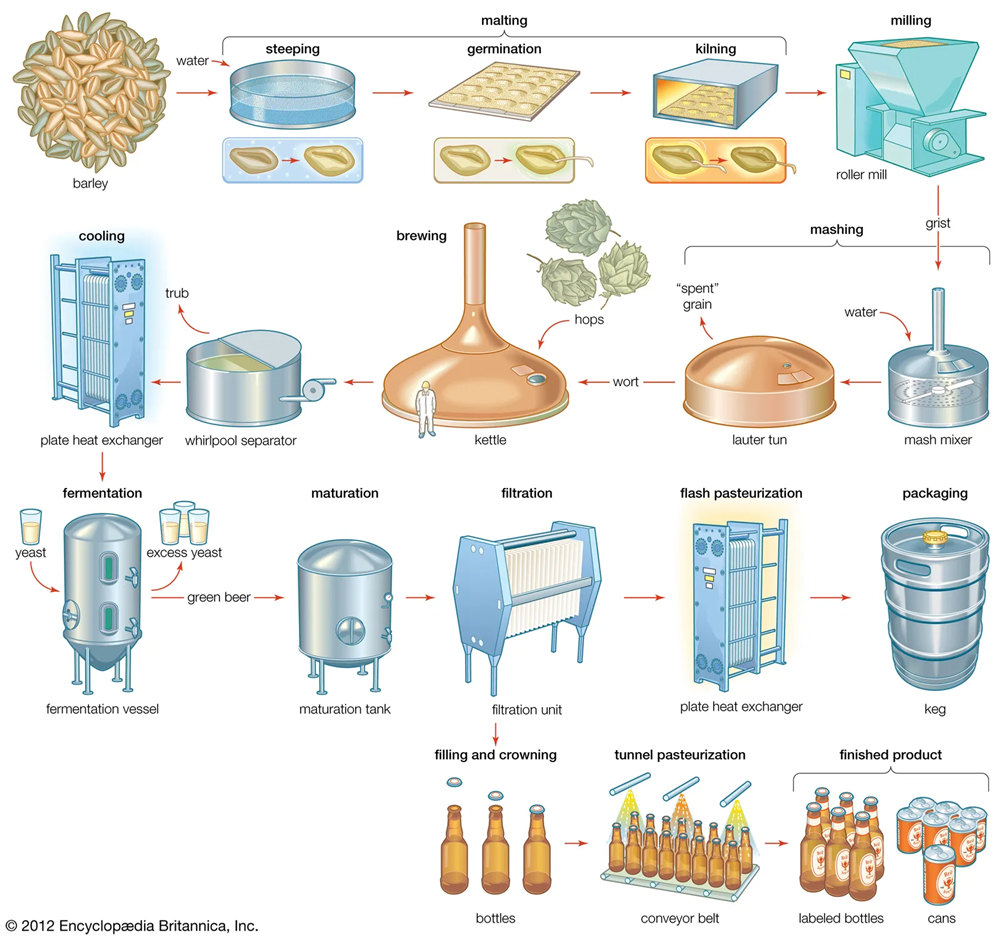
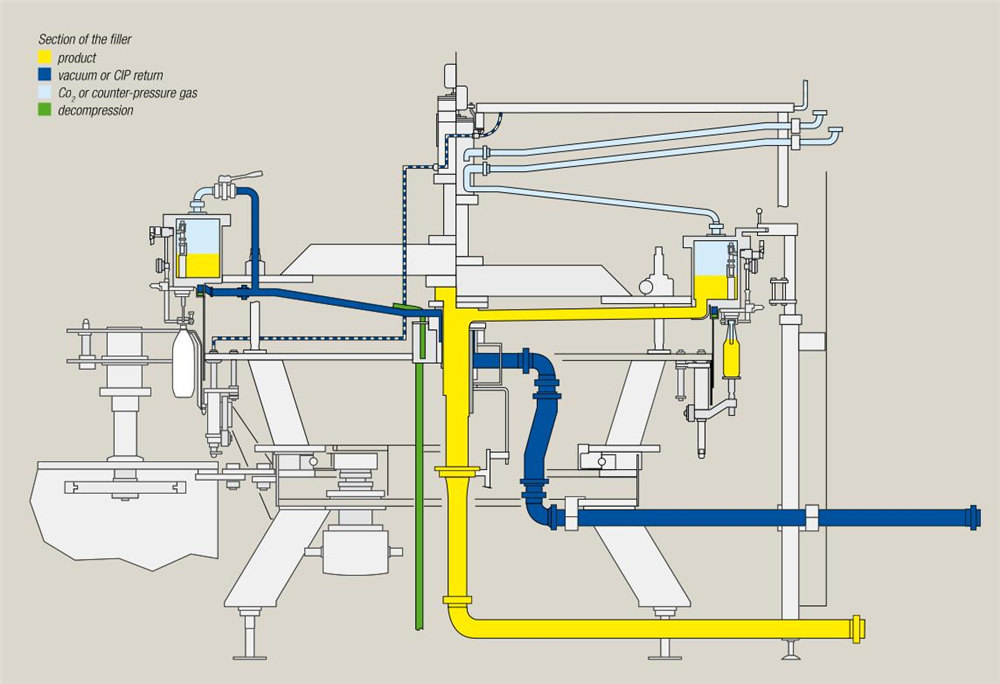
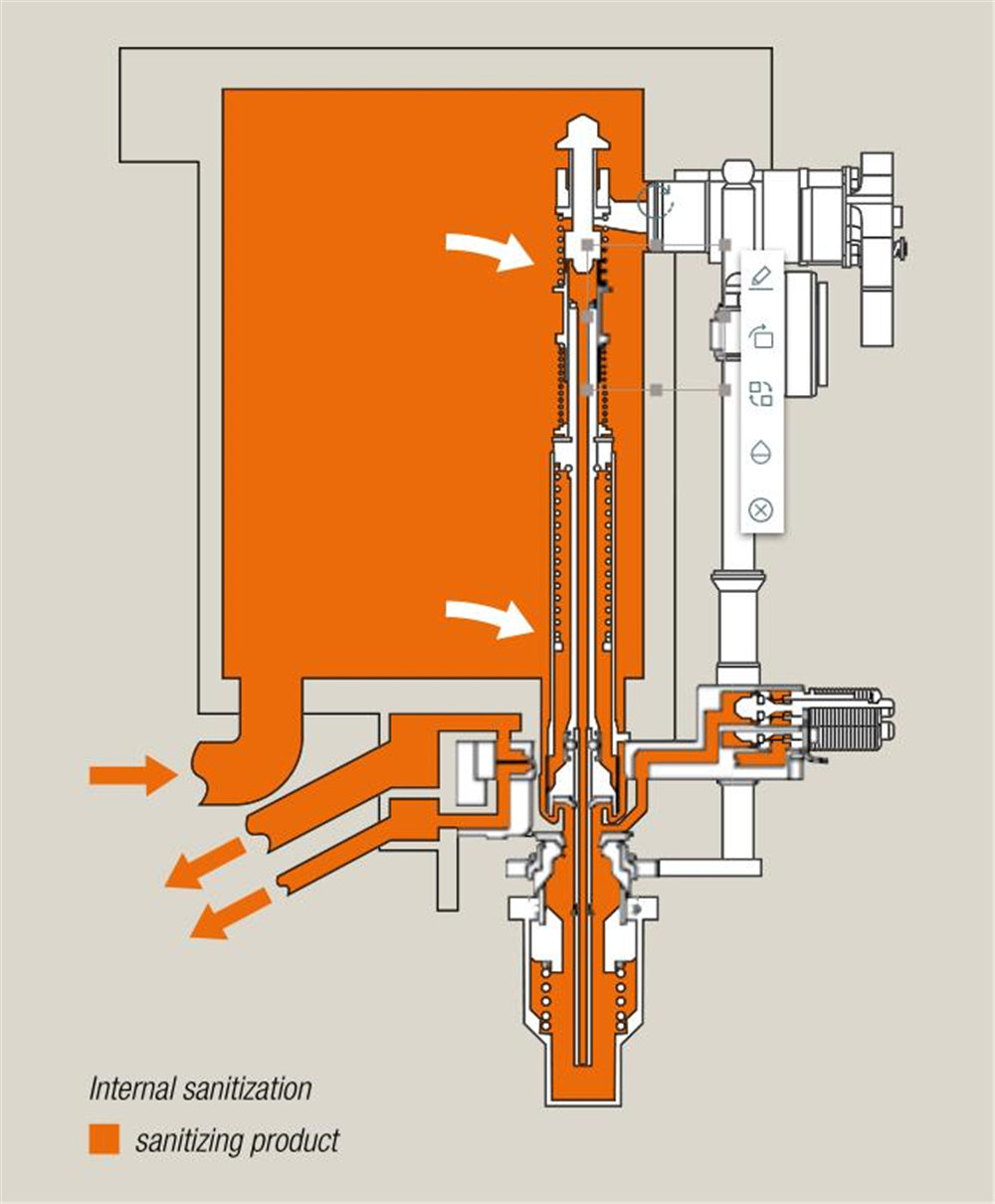
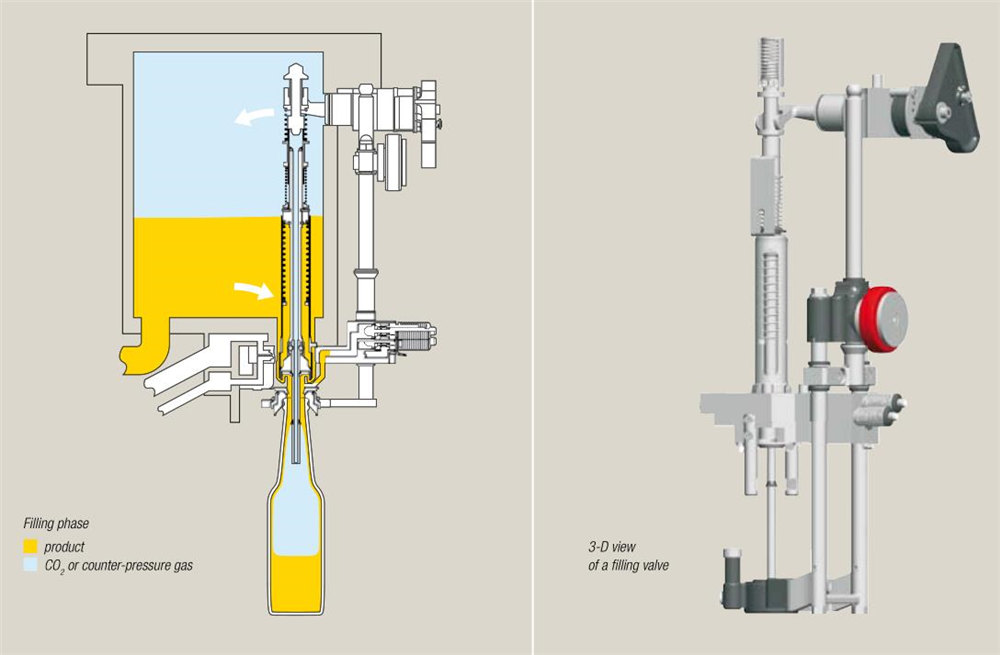
Technical Specfication
Type | Production capacity (BPH) | Pitch circle diameter | size | |
JH-PF14-12-5 | 1500-2000/(500ml) | Φ600 | ||
JH-PF24-18-6 | 2500-3500 | Φ720 | ||
JH-PF32-24-8 | 3500-4500 | Φ960 | ||
JH-PF40-32-10 | 7000-8000 | Φ1120 | ||
JH-PF50-40-12 | 10000-12000 | Φ1400 | ||
JH-PF60-50-15 | 13000-16000 | Φ1500 |